Top 50 Organizational Improvement Acronyms
The team at Transformance Advisors combined our experience with input from other experts to create this list of the top 50 organizational improvement acronyms. The candidates came in like an endless freight train blocking your way to an important meeting. We debated, scored, and settled on the best of the best. These are the top 50 acronyms you need to know!
Make this page a favorite and come back to:
- Find the right acronym for your presentation to the board of directors
- Settle a dispute with a less-informed colleague
- Prepare for an exam
- Gain inspiration for the next time you play Acronymity
Acronym | Term | Definition | Link |
---|---|---|---|
3P | Production, Preparation, Process | A Lean methodology which drives dramatic improvements in product and process design by developing multiple approaches and selecting the best choice based on which design has the least waste. | Lean Thinking and Methods – 3P |
5S | The 5S System | A systematic approach to create and maintain workplace organization using the steps sort, stabilize, shine, standardize, and sustain (or some version of those words). Some advocates of Lean suggest this is a fast and easy thing you should do right away. Others will caution how the standardize and sustain steps are challenging and you should avoid starting a Lean program with a failure. | 5S Failure |
8D | Eight Disciplines Problem Solving | An eight step problem solving methodology designed to identify, correct, and eliminate recurring problems, making it useful in product and process improvement. | Eight Disciplines Problem Solving |
A3 | A3 Problem Solving | A systematic five step process for solving complex problems where the root cause is not obvious. The best approach leverages two critical roles of coach and problem solver. A3 comes from a special size of paper which is not common in the United States. The uninformed will often claim A3 Problem Solving is a simple process which only requires one piece of paper, one pencil, and one eraser. | Why Do A3 Efforts Fail? |
AI | Artificial Intelligence | A method of making a computer, a computer-controlled robot, or a software program think intelligently like the human mind. AI is accomplished by studying the patterns of the human brain and by analyzing the cognitive process. Many technologies have emerged which allows AI-based programs to assist with writing resumes, summerizing research, solving math problems, writing code, and creating images. There are four types of artificial intelligence: reactive machines, limited memory, theory of mind and self-awareness. | Artificial Intelligence |
Acronym | Term | Definition | Link |
---|---|---|---|
ANOVA | Analysis of Variance | An approach to comparing data with multiple means across different groups, allowing you see patterns and trends within complex and varied data. It can be used to mathmatically verify correlation and root cause. The scientific method relies on ANOVA, since creating an experiment, gathering data, and performing statistical analysis on the results is key to hypothesis testing. | Analysis of Variance |
BI | Business Intelligence | A program which combines business analytics, data mining, data visualization, data tools and infrastructure, and best practices to help organizations make data-driven decisions. | Business Intelligence |
CI | Continuous Improvement | The routine and incremental improvement, to a process, which enhances stakeholder value or responds to environmental change. | What is Continuous Improvement? |
CLA | Certified Lean Apprentice | A credential which indicates a person has learned the principles, concepts, and terms which everyone “must understand” in any organization seeking to make a Lean Transformation. A Lean Apprentice will be a valuable project team member able to help analyze value streams, identify waste, design and implement improvements, and promote continuous improvement. | Certified Lean Apprentice |
CLE | Certified Lean Expert | A credential which indicates a person has learned and gained hands-on experience solving complex problems. A Lean Expert will be able to address complex problems by articulating the situation, identifying the root cause, crafting countermeasures, and leading the implementation of improvements. | Certified Lean Expert |
Acronym | Term | Definition | Link |
---|---|---|---|
CLM | Certified Lean Master | A credential which indicates a person is able to navigate the cultural challenges with leading a Lean Transformation. A Lean Master will be able to design and lead the Lean Transformation program for an organization. | Certified Lean Master |
CLP | Certified Lean Practitioner | A credential which indicates a person has learned and gained hands-on experience with the most powerful tools used for Lean Transformations. A Lean Practitioner will be able to manage projects, lead value stream mapping sessions, identify waste, design and implement improvements, and promote continuous improvement. | Certified Lean Practitioner |
CSSBB | Certified Six Sigma Black Belt | A credential which indicates a person has learned and gained hands-on experience with the methodology and advanced tools used for Six Sigma projects. A Six Sigma Black Belt will lead major projects, ensure rigorous data analysis, coach teams in designing robust solutions, guide implementation of improvements, and monitor new processes until they are ingrained. | Certified Six Sigma Black Belt |
CSSGB | Certified Six Sigma Green Belt | A credential which indicates a person has learned and gained hands-on experience with the methodology and tools used for Six Sigma projects. A Six Sigma Green Belt will be able to manage projects, collect data, analyze data, design and implement improvements, and promote continuous improvement. | Certified Six Sigma Green Belt |
CSSYB | Certified Six Sigma Yellow Belt | A credential which indicates a person has learned the principles, concepts, and terms which everyone “must understand” in any organization using the Six Sigma improvement methodology. A Six Sigma Yellow Belt will be a valuable project team member able to help collect data, analyze data, design and implement improvements, and promote continuous improvement. | Certified Six Sigma Yellow Belt |
Acronym | Term | Definition | Link |
---|---|---|---|
DFSS | Design for Six Sigma | A collection of best-practices for the development of new products and processes leveraging the Six Sigma philosophy. The objective is to determine the needs of customers and the business, and driving those needs into the new solution us steps often refered to as Define, Measure, Analyze, Design, and Verify. | Design for Six Sigma |
DMAIC | Define, Measure, Analyze, Improve, and Control | The 5 steps of the Six Sigma methodology. | What is Six Sigma? |
EQ | Emotional Quotient | The ability to manage both your own emotions and understand the emotions of people around you. There are five key elements: self-awareness, self-regulation, motivation, empathy, and social skills. | What is Emotional Intelligence? |
FMEA | Failure Mode and Effects Analysis | A structured approach to discovering potential failures that may exist within the design of a product or process. Failure modes are the ways in which a process can fail. Effects are the ways these failures can lead to waste, defects, or harmful outcomes for the customer. Failure Mode and Effects Analysis is designed to identify, prioritize and limit these failure modes. | Failure Mode and Effects Analysis |
HFS | High Flexibility Scheduling | A program of integrated processes for Supply Planning, Master Scheduling, and Detail Scheduling whereby you “plan to a forecast” and “execute to an order”. The term and acronym were coined by George Jones when he led the transformation of planning and scheduling processes at Sweetheart Cup Company. | What is High Flexibility Scheduling? |
Acronym | Term | Definition | Link |
---|---|---|---|
IPA | Improvement Program Assessment | A systematic process for collecting, analyzing, and acting on information about the effectiveness of an organization’s chosen improvement program. | Improvement Program Assessment |
JIT | Just-in-Time | A management philosophy focused on producing goods or services only based on customer demand. There is a focus on efficiency, productivity, reduction of waste, and continuous improvement. | Just-in-Time Manufacturing |
KPI | Key Performance Indicator | A performance measurement or metric that is thought to be a critical measure of success for an enterprise. Key Performance Indicators can be qualitative or quantitative in nature, and ideally, a leading indicator of progress. They can be dangerous when they drive individuals make the numbers look good regardless of the consequences. | Performance Indicator |
LCL | Lower Control Limit | On a control chart, the lower control limit is a line below the centerline which indicates a process is out of statistical control due to special cause variation. In traditional Statistical Process Control, it is typically set to three standard deviations below the mean. | Control Charts |
LSS | Lean Six Sigma | A term with no clear meaning in the world of organizational improvement. It’s meant to sound like a hybrid program using Lean and Six Sigma. Most often, it is 95% Six Sigma with 5% Lean thrown in for good measure. Recent indications point to a race to the bottom where people do their own thing and call it Lean Six Sigma. They cut corners on the DMAIC steps from Six Sigma and don’t work the cultural transformation aspect from Lean. | What is Lean Six Sigma? |
Acronym | Term | Definition | Link |
---|---|---|---|
MSA | Measurement System Analysis | A process used to evaluate the suitability of a measuring system for use. Key steps in the process are determining whether the correct measurement is being used, assessment of the measuring device, assess the personnel’s ability to effectively execute the measurement system instructions, identify any environmental factors that might affect the process, and calculate if all this variation means the current measurement system needs an overhaul. | What Is Measurement System Analysis? |
MVP | Minimum Viable Product | A version of a new product with just enough features to be usable by early customers who can then provide feedback for further development. A minimum viable product has just enough core features to effectively deploy the product, and no more. It is typically deployed to a subset of possible customers, such as early adopters who are thought to be more forgiving, more likely to give feedback, and able to grasp a product vision from an early prototype or marketing information. | Minimum Viable Product |
OEE | Overall Equipment Effectiveness | A powerful performance measurement derived from three elements: availability, performance, and quality. Measuring Overall Equipment Effectiveness is a best practice and very common in organizations leveraging improvement programs such as Six Sigma or Lean Transformation. | What is OEE? |
OpEx | Operational Excellence | An approach to business management that emphasizes continuous improvement across all aspects of the business and within all business processes by creating a culture where management and employees are invested in business outcomes and empowered to implement change. | Operational Excellence |
PDCA | Plan, Do, Check, Act | A problem solving tool used for continious improvement which leverages the scientific method concepts of hypothesis, experiment, and evaluation. | What is PDCA? |
Acronym | Term | Definition | Link |
---|---|---|---|
PERT | Program Evaluation and Review Technique | A project management methodology that visually represents the time it takes to complete a project. At its core, PERT utilizes a network of diagrams to visually illustrate the sequence of activities and milestones in a project timeline. One powerful aspect is identifying the sequence of activities which control the estimated time of a project from start to finish. This sequence is called the critical path. | What Is PERT In Project Management? |
QFD | Quality Function Deployment | A structured approach and set of tools used to define customer requirements and convert them into detailed specifications and plans to produce the products and services which fulfill those requirements. | What is QFD? |
QMS | Quality Management System | A formal set of policies, procedures, and process established to ensure products and services meet customer expectations. An effective Quality Management System (QMS) provides the means to consistently meet consumer expectations and deliver products and services with minimal waste. | What is QMS? |
RACI | Responsible, Accountable, Consulted, Informed | A diagram used in project management to define team roles across 4 categories: Responsible, Accountable, Consulted, and Informed. It helps clarify who does the work, who calls the shots, whose opinion matters, and who needs to stay in the loop for each task, milestone, or decision. | Responsibility Assignment Matrix |
RCA | Root Cause Analysis | Taking an issue, which needs to be addressed, and finding the root cause of the issue. The goal is to get to the source of the problem by focusing on the underlying causes of problems rather than simply treating the symptoms. | Root Cause Analysis |
Acronym | Term | Definition | Link |
---|---|---|---|
ROI | Return on Investment | A performance measure used to evaluate the efficiency or profitability of an investment. The benefit (or return) of an investment is divided by the cost of the investment and the result is expressed as a percentage. In project management, return on investment is used to quantify the financial benefits of the project vs. the cost and is often a key element in the approval to proceed. | Lean Project Scorecards |
RPN | Risk Priority Number | A technique for analyzing the risk associated with potential problems identified during a Failure Mode and Effects Analysis (FMEA). It is a calculated value of risk assigned to a failure mode most often using Severity (of the event) × probability (of the event occurring) × detection (before failure reaches the user/customer}. | Failure Mode and Effects Analysis |
S&OP | Sales & Operations Planning | A process to strategically direct an organization to competitive advantage through effective management of demand and supply. | Sales and Operations Planning |
SCM | Supply Chain Management | The management of a network of interconnected organizations engaged in the provision of product and service packages required by the ultimate consumer. | What is Supply Chain Management? |
SIPOC | Suppliers, Inputs, Process, Outputs, and Customers | A tool used to summarize the inputs and outputs of a value stream or process. It specifies the Suppliers, Inputs, Process, Outputs, and Customers and can be quite useful to set the boundaries of a process before you create a value stream map or a process map. | What is SIPOC? |
Acronym | Term | Definition | Link |
---|---|---|---|
SMART | Specific, Measurable, Attainable, Realistic, Time-Based (Goals) | A guide for setting meaningful goals for projects, teams, and people using the 5 criteria of Specific, Measurable, Attainable, Realistic, and Time-Based. | How to Write SMART Goals |
SMED | Single Minute Exchange of Dies | A systematic approach to reduce changeover time, with the original focus on changing dies for stamping equipment. Today’s more inclusive terminology refers to this as changeover reduction. | What is Changeover Reduction? |
SOP | Standard Operating Procedure | The sequence of activities, or set of actions, which is the official, or accepted, way of doing something. Essentially, a procedure is how a process needs to be done. It ensures you get a consistent outcome. | Policies, Procedures, and Work Instructions |
SPC | Statistical Process Control | The application of statistical methods to monitor and control a process. Data is collected in the form of product or process measurements or readings from various machines or instrumentation. It is a scientific visual method to monitor, control, and improve the process by eliminating special cause variations. | Control Charts |
SWOT | Strengths, Weaknesses, Opportunities, and Threats | A means to organize key aspects of almost anything into the categories of Strengths, Weaknesses, Opportunities, and Threats. You can develop a listing of these characteristics for an organization, a department, a process, a product or service, at team, or an individual (you!). Strengths and weaknesses are internally focused while Opportunities and Threats bring in an outside perspective. | What is SWOT Analysis? |
Acronym | Term | Definition | Link |
---|---|---|---|
TPM | Total Productive Maintenance | A holistic approach to equipment maintenance that strives to achieve perfect production. The focus is on no breakdowns, no small stops, no slow running, no defects, and no accidents. It blurs the distinction between the roles of production and maintenance by placing a strong emphasis on empowering operators to help maintain their equipment. | Lean Thinking and Methods – TPM |
TQM | Total Quality Management | A management approach that focuses on delivering products and services with the highest quality to maximize customer satisfaction and meet regulatory standards. Total Quality Management is an organization-wide effort for continuous improvement. | Total Quality Management |
UCL | Upper Control Limit | On a control chart, the upper control limit is a line above the centerline which indicates a process is out of statistical control due to special cause variation. In traditional Statistical Process Control, it is typically set to three standard deviations above the mean. | Control Charts |
VOC | Voice of the Customer | A detailed set of customer wants and needs, organized into a hierarchical structure, and then prioritized in terms of relative importance and satisfaction with current alternatives. Voice of the Customer typically consists of both qualitative and quantitative research and is generally conducted at the start of any new product, process, or service design initiative. | Voice of the Customer |
VSM | Value Stream Map | A visual representation of activities and flows of information, materials, and services required to accomplish specific objectives. | What is Value Stream Mapping? |
Send us your favorite acronyms.
Get the Transformance Communiqué
“the newsletter for those crafting a sustainable organization”
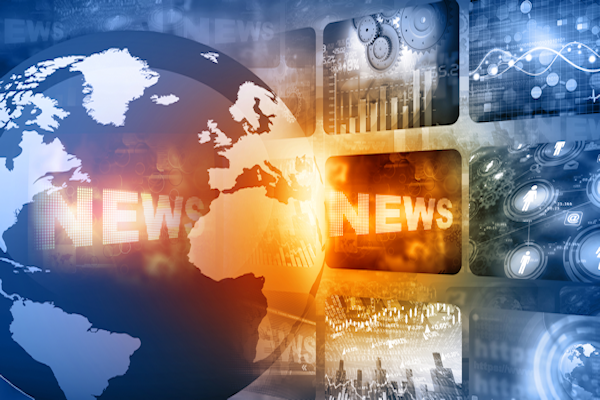