Comprehensive Lean Program
A Lean Transformation program is one of the best investments any organization can make. The return on investment (ROI) is better than many other strategic initiatives. Eliminating waste will improve customer satisfaction, increase revenue (or impact), and reduce costs.
Our comprehensive Lean Transformation program provides your team with all the tools and knowledge required to craft a sustainable organization. We significantly improve your ROI by compounding the synergistic effects of three critical components:
- Lean Projects: Our research and experience has revealed the key to success is executing well-defined Lean projects. These projects must engage employees to eliminate waste and deliver significant improvements.
- Continuous Improvement: Lean projects will provide you better and stable processes. This is the time to leverage continuous improvement to keep getting better and respond to the constant change swirling around you.
- Program Management: Maintaining a portfolio of improvement projects, communicating the exciting accomplishments, dealing with change management, and providing educational events for everyone are just some of the requirements for a successful Lean Transformation. You need a champion focused on your Lean Transformation program.
While each of the above components provide great value, it is the synergy between them which makes for a successful Lean Transformation. Your ability to craft a sustainable organization is far more likely when you have all pieces of the puzzle than with any alternative approach.
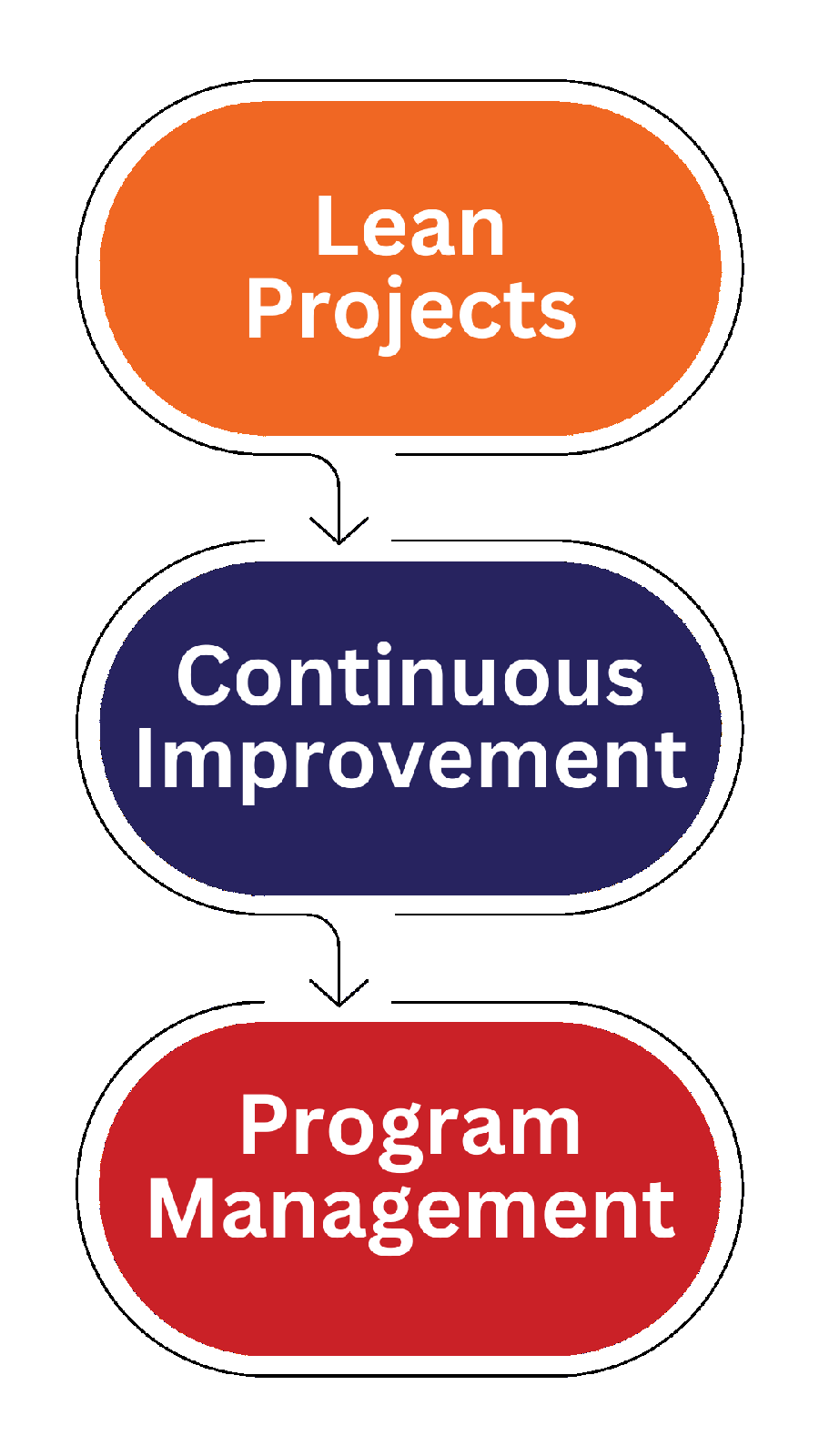
A sustainable organization “achieves its mission while meeting the needs of the present without compromising the future”.
Top 5 Benefits of a Lean Transformation Program
Return on Investment (ROI)
The investment in a Lean Transformation program is relatively modest. It takes time and money for Lean projects, continuous improvement, and program management. The results, or return, can be astonishing.
Thus, astonishing return divided by modest investment = outstanding ROI.
A few of your results could be:
- Reduce the cycle time for new product development creating faster time to market and increased revenue.
- Reduce defects and wasted effort creating more efficient processes with reduced cost.
- Improve service and quality leading to impressed customers and increased revenue.
- Cut down on mistakes and miscommunication creating a better quality of life with fewer hassles and firefighting.
- Create stable processes which don’t rely on tribal knowledge and can scale up for growing revenue.
- Develop empowered employees with a common language able to drive continuous improvement.
- Reduce the waste of energy and materials lowering your carbon footprint and delivering on your sustainability goals.
A Lean Transformation program delivers results. There is a reason Lean is the #1 improvement program in the world.
Quality of Life
Low morale, low productivity, and high turnover plague many organizations. Processes rely on tribal knowledge and firefighting. Processes breakdown when there is the smallest disruption. There are too many hassles, the ship is sinking, and quality of life is low.
It does not have to be that way. A Lean Transformation program will create processes which are stable, flexible, and able to meet stakeholder needs. Empowered employees will focus on data-driven decisions and leverage systematic methodologies which will mean problems get solved and don’t keep coming back. No more whack-a-mole.
Scalability
Processes which rely on tribal knowledge and firefighting will hold an organization back. Many find they cannot grow as everything seems to break at the slightest increase in customer demand.
It’s very common for an organization to grow to a point where the old processes no longer work and it’s time for a significant upgrade. This is the ideal time for a Lean Transformation. It’s time to understand what works and doesn’t work with the current state. The next step is to create a better future state which leverages best practices and is scalable.
Lean more about reaching the points where it’s time to upgrade your processes at: 7 Stages of Growth.
Sustainability
The goal of a Lean Transformation is to craft a sustainable organization which “achieves its mission while meeting the needs of the present without compromising the future”.
The greatest benefit from undertaking a Lean Transformation is fulfilling the mission of your organization in a manner which protects planet earth and all stakeholders.
Community
Lean is the #1 improvement program for a reason. As the most popular and best improvement program, there is a large community of organizations and individuals on the same journey as you. This brings a number on advantages:
- The tools exist and you don’t have to recreate the wheel or waste resources developing new methodologies or new classes
- You will develop a common language, built around the elimination of waste, creating empowered employees able to drive continuous improvement
- You will join those organizations who proudly claim they are members of the Lean community, creating a competitive advantage
- You will recruit better candidates with Lean experience and won’t be fooled by those who have only been chaotic cost cutters
Lean more at: What is Lean?
3 Components of a Lean Program
As identified above, we have 3 components required for an effective Lean Program:
- Lean Projects
- Continuous Improvement
- Program Management
Let's look closer at each one.
1. Lean Projects
Lean is defined as "the systematic elimination of waste". Lean projects are very systematic. You start with a project scorecard to identify the great projects and reduce your risk of working on low value projects. Part of the scorecard will evaluate which type of Lean project you are looking at. Value stream mapping is one of the most effective. Other types include changeover reduction, problem solving, and the 5S System. Each type of Lean project has it's unique and systematic steps which are the key to success.
The 5 Principles of Lean are: Specify Value, Identify Value Streams, Create Flow, Leverage Pull, and Seek Perfection. Lean projects put the principles, or fundamental truths, into practice. Through the systematic application of these principles, your Lean projects will focus on value, as specified by stakeholders, and eliminate waste in all value streams.
Another part of the scorecard will determine the availability of resources. One very important role is the Project Champion. This is the person who owns the leadership role and delegates the project management role. A Lean Transformation is not some bottom-up magical metamorphosis where the leadership team spends their days on the golf course. Effective project champions are critical for successful projects and are thus critical for the success of a Lean Transformation.
At Transformance Advisors, the framework for learning, and applying the Lean tools, is built into our project-based training courses. These courses provide the right level of knowledge and skills for everyone in your organization.
For more information on improvement projects, see:
Lean is "the systematic elimination of waste".
2. Continuous Improvement
Before closing out a Lean project, the process needs to transition into the mode of continuous improvement. No project will create perfection and constant change means a process needs to be changing to meet the new realities.
Leveraging the right performance measurements will signal where a process needs adjustment. Empowered employees will get to the root cause of issues and use techniques, such as kaizen blitz events and "Plan Do Check Act", to create a culture of continuous improvement.
Beyond empowered employees, continuous improvement is also facilitated by leadership, supervisors, and other stakeholders getting out where the action takes place by leveraging the concept of gemba walks. A gemba walk is a walking visit to the actual place where value is created, with a goal to observe, listen, learn, and help. It is not a presentation in a conference room or a quick meeting in front of some performance reporting station.
Routine process audits will also help to maintain the gains and promote additional improvement. The 5S System has a special step for audits and this concept can be applied across the organization. These audits ensure "standard work" becomes the norm for achieving an intended outcome, while providing a baseline for continuous improvement.
For more information on continuous improvement, see:
Continuous improvement is "the routine and incremental improvement, to a process, which enhances stakeholder value or responds to environmental change".
3. Program Management
An effective Lean Transformation will have a solid foundation supporting the Lean projects and continuous improvement activities. You need someone, or a small team, with the time and ability to:
- Promote the goal
- Establish priorities
- Communicate progress
- Deal with challenges
- Manage the budget
- Make course corrections
The exciting goal for a Lean Transformation is to create a sustainable organization capable of achieving your mission. People want to be on a mission. No one gets excited about cutting costs (and revenue) to zero.
In most cases, you can't do everything at once. People are busy. Priorities need to be established and should drive the criteria in your project scorecard.
Communicating progress on the priorities and dealing with challenges are also part of program management. You will start with the "low hanging fruit" providing fast and amazing results. The transition to the harder and bigger cross-functional challenges will require more effort and skills to produce even greater results.
Capturing the incredible ROI of a Lean Transformation requires the "investment" in developing people through education and funding Lean projects and continuous improvement activities to find and eliminate waste. Part of program management is to manage the budget to ensure "investments" are made and the "return" part of ROI is achieved.
A final part of program management is taking time to "step back to reflect" on the effectiveness of your Lean Transformation program. One excellent approach is to conduct an annual improvement program assessment and use the findings to make course corrections.
For more information on program management, see:
FAQs on What's Involved with a Lean Transformation?
How do I know if my organization needs a Lean Transformation?
One easy way to recognize the need for a Lean Transformation is to look at and listen to what's happening everyday. Common buzzwords or phases you might notice are:
- Challenges are confronting everyone. You are on defense all the time.
- Firefighting is the routine. Your best people are firefighters.
- Problem-Solving is fine, except when you keep solving the same problems over and over again.
- Confusion is driving people crazy. What should we do? Who should do something?
- Miscommunication leads to errors. I thought someone else was taking care of that.
- Room for Growth means you are not growing. Tribal knowledge is not effective and processes are sluggish.
You can learn more at: Recognizing the Need for a Lean Transformation.
Isn't Lean just about making small improvements every day?
Making small improvements every day is just one part of Lean. As one of the easier things to do, some people choose to focus on it and ignore the higher value parts of a Lean Transformation.
Value steam mapping, problem solving, changeover reduction, the 5S System, and other Lean tools deliver big benefits. These are not small efforts where you spend 2 minutes a day.
Lean is the #1 improvement program in the world. The wide variety of tools and common sense indicates there is more to it than just making small improvements every day.
Those who only work 2 minutes a day are picking up pennies and stepping over bushel baskets of dollars.
You can learn more at: What is Lean?
We trained employees on some Lean tools and saw minor success in cutting costs. What should we do different?
We define Lean as "the systematic elimination of waste". Unfortunately, Lean tools are often used for chaotic cost cutting and the results are always less than what can be achieved by focusing on waste.
It takes a change in thinking to focus on waste. Do you try to cut the cost of gasoline or do you stop wasting time and gasoline by combining trips or car pooling?
It often takes more training on Lean thinking vs. overdoing the training on Lean tools. You want to use the tools to eliminate waste. Don't use the tools for chaotic cost cutting.
Using the tools correctly will come when you have the three components of a Lean Transformation in place. You need Lean projects, continuous improvement, and program management.
We have hired multiple people with Lean experience and they all have a different philosophy and approach. How can this be?
The good news is how Lean is the #1 improvement program in the world. The bad news is how there are different flavors of Lean all over the world.
If you have hired a number of people with Lean on their resume, then chances are you have introduced variation, and possibly some chaos, into your organization. Some places think Lean is just about continuous improvement and you do simple things for 2 minutes every day. The worst organizations will use the Lean tools for chaotic cost cutting.
Regardless of their background with Lean, you need to ensure all new hires are educated on your Lean Transformation program. You should even look at sending the new hires through the same Lean training courses you use for those without any experience with Lean.
You can learn more at: What is Lean?
Should we do Lean Six Sigma instead?
Research into Lean Six Sigma reveals it is much more about Six Sigma and tends to have very little about the rich features of a Lean Transformation. Lean Six Sigma adherents will often treat Lean as a collection of tools, you can use when you work on a Six Sigma project.
Descriptions of Lean Six Sigma will often place a strong emphasis on using the Define, Measure, Analyze, Improve, and Control (DMAIC) methodology. This methodology is big for Six Sigma projects and not very common for Lean projects.
If you want to do Lean, the #1 improvement program in the world, then do Lean. Don't do Lean Six Sigma.
You can learn more at: What is Lean Six Sigma?
Can I just buy a magic pill which will optimize everything with no effort from our leadership team?
No!
It's going to take a commitment from your leadership team.
Lean looks like the solution we have been searching for. What should I do first?
First give yourself a pat on the back for realizing Lean can be transformative for your organization.
Your next step is to contact us. We will help you assess your opportunities and craft a roadmap to success.
Putting a Lean Program all Together
Lean projects, continuous improvement, and program management are the three critical components for a successful Lean Transformation program. They provide the necessary ingredients required to craft a sustainable organization which can deliver on your mission.
Lean projects provide a systematic approach for eliminating waste and establishing better more stable processes. These projects will make significant improvements in areas such as increased revenue, decreased costs, and improved quality of life.
Continuous improvement can be applied to a stable process to create even better performance and react to changes in the workplace. Similar to a 401k program, small incremental improvements will build over time and provide enormous returns on the investments made.
Program management provides the supporting infrastructure for Lean projects and continuous improvement to thrive. It will keep the focus on the right priorities.
A Lean Transformation program is a great investment and provides incredible ROI. Lower your risk and increase your chances of success by doing it right.
Is it time to craft a sustainable organization?
A Lean Transformation is "the systematic elimination of waste with the goal of crafting a sustainable organization".
FAQs on Why Transformance Advisors for help with a Lean Transformation?
Why is your approach better than the others?
Research and experience have taught us the 3 critical components of a Lean Transformation are Lean projects, continuous improvement, and program management. We will help you focus on the right things and avoid the common traps which derail too many enthusiasts.
We have a complete package of educational events and coaching to help your team learn what to do and receive help doing what needs to be done.
Just ask the others what it takes to achieve success and you will probably get long rambling answers which bore you silly.
Lean more about the common traps waiting to derail you at: The 5 Horrors of Lean.
How are your classes better than other options?
Our classes are focused on the various roles different people will own as part of a Lean Transformation program. Almost everyone will be project team members and help with continuous improvement. Others will lead value stream mapping projects, problem solving efforts, or other types of projects. A relatively few will have leadership roles and responsibility for overall program management.
Our family of training and certification programs includes:
Lean Apprentice is designed for everyone at an organization which is pursuing a Lean Transformation.
Lean Practitioner provides hands-on experience leading a value stream mapping project.
Lean Expert provides hands-on experience leading a problem solving project.
Lean Master explores program management including an assessment and development of a roadmap to success.
Beyond great education and immediate application, many of our classes provide individuals the opportunity to earn professional credentials. These credentials demonstrate expertise and a commitment to continuous education.
You can learn more at: Lean Education Standards and Top 5 Reasons to Earn a Certification.
How does your program help me manage risk?
We start with education which includes immediate application of the concepts on a Lean project. You will begin with value stream mapping, which has the best overall success rate for any type of project. Many of these initial classes and projects deliver big results in terms of better processes which increase revenue, lower costs, and improve the quality of life for everyone.
You start small and achieve success.
You do not shut down the entire facility for 2 days and then release people to wonder what to do next. You do not have someone spend months creating training materials which don't meet the challenge at hand.
Most importantly, you do not fall into one of the common traps, which are described in: The 5 Horrors of Lean.
Why shouldn't we just hire someone with Lean experience and let them run our program?
The good news is Lean is the #1 improvement program in the world. The bad news is there are millions of people with Lean on their resume and very few have been part of a successful Lean Transformation.
If you hire someone with Lean on their resume, then you might only bring chaos into your organization. Some places think Lean is just about simple improvement things done for 2 minutes every day. The worst organizations will use the Lean tools for chaotic cost cutting.
A better approach, with less risk and a much higher probability of success, is to designate one of your key people to become the Lean Champion. They know your organization, products, customers, suppliers, and processes. Your Lean Champion can work with our team at Transformance Advisors to achieve success by focusing in the three critical components of Lean projects, continuous improvement, and program management.
Can I just buy a magic pill which will optimize everything with no effort from our leadership team?
No!
We remove the confusion and endless references to Japanese words. But, it's still going to take a commitment from your leadership team.
Your program looks like the solution we have been searching for. What should I do first?
First, give yourself a pat on the back for realizing Lean can be transformative for your organization.
Your next step is to contact us. We will help you assess your opportunities and craft a roadmap to success.
Contact Us
Get the Transformance Communiqué
"the newsletter for those crafting a sustainable organization"
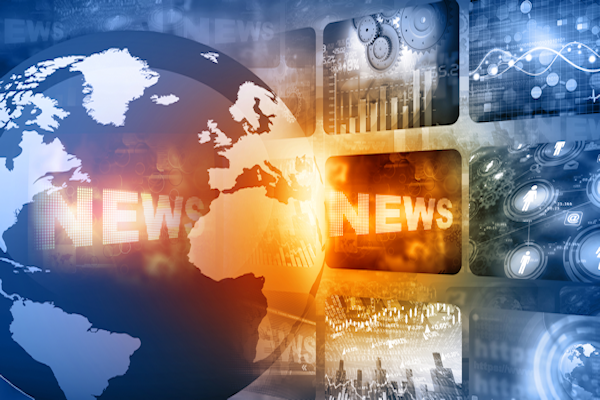
References
What is Lean Transformation? by Liz Llewellyn-Maxwell.