Top 50 Organizational Improvement Terms
The team at Transformance Advisors combined our experience with input from other experts to create this list of the top 50 organizational improvement definitions. The candidates came in like an endless line of people waiting to get into a Taylor Swift concert. We debated, scored, and settled on the best of the best. These are the top 50 terms you need to know!
Make this page a favorite and come back to:
- Find the right word for your presentation to the board of directors
- Settle a dispute with a less-informed colleague
- Prepare for an exam
- Gain inspiration for your daily Wordle challenge
Term | Definition | Link | Acronym |
---|---|---|---|
5 Whys | Asking and answering “Why” five times is expected to lead to the root cause of a recurring issue. It may take more or less than 5, but the spirit is to dig deeper as the first couple of answers are often nowhere near the root cause. | Root Cause Analysis | |
A3 Problem Solving | A systematic five step process for solving complex problems where the root cause is not obvious. The best approach leverages two critical roles of coach and problem solver. A3 comes from a special size of paper which is not common in the United States. The uninformed will often claim A3 Problem Solving is a simple process which only requires one piece of paper, one pencil, and one eraser. | Why Do A3 Fail? | A3 |
Agile | An umbrella term for a set of frameworks and practices based on the values and principles expressed in the Manifesto for Agile Software Development and the 12 Principles behind it. Agile software development is more than frameworks such as Scrum, Kanban, Extreme Programming, or Feature-Driven Development (FDD). Agile software development is more than practices such as pair programming, test-driven development, stand-ups (daily meetings), sprint planning, and sprints (iterations). | What is Agile? | |
Balanced Scorecard | A tool designed to track more than just financial metrics by adding additional perspectives which focus on customers, internal business processes, and learning and development. These additional perspectives help businesses measure all the activities essential to creating value. | What is a Balanced Scorecard? | |
Best Practice | A procedure, demonstrated by research and experience, which produces superior results and is suitable for widespread adoption as a standard. | Bashing Best Practices |
Term | Definition | Link | Acronym |
---|---|---|---|
Business Intelligence | A program which combines business analytics, data mining, data visualization, data tools and infrastructure, and best practices to help organizations make data-driven decisions. | Business Intelligence | BI |
Change Management | The process of guiding organizational change to fruition, from the earliest stages of conception and preparation, through implementation and, finally, to resolution. | Change Management Process | |
Changeover Reduction | A systematic approach for reducing the period required to change from producing the last good product or service of one batch to producing the first good product or service of the next batch. | What is Changeover Reduction? | |
Changeover Time | The period required to change from producing the last good product or service of one batch to producing the first good product or service of the next batch. | What is Changeover Reduction? | |
Continuous Improvement | The routine and incremental improvement, to a process, which enhances stakeholder value or responds to environmental change. | What is Continuous Improvement? | CI |
Term | Definition | Link | Acronym |
---|---|---|---|
Control Chart | Statistical and graphical methods which give you a look at what’s happening inside any process. These charts can help you identify any remaining, or brand new, process performance issues. | Control Charts | |
Define, Measure, Analyze, Improve, and Control | The 5 steps of the Six Sigma methodology. | What is Six Sigma? | DMAIC |
Empowered | Allowing employees to make independent decisions and take action as they see fit. | What is Lean? | |
Gemba | A Japanese word for “the actual place”. All across the world, lean enthusiasts think of the gemba as the actual place where value is created. | Gemba Walkers | |
Gemba Walk | A walking visit to the actual place where value is created, with a goal to observe, listen, learn, and help. | Gemba Walkers |
Term | Definition | Link | Acronym |
---|---|---|---|
Improvement Program Assessment | A systematic process for collecting, analyzing, and acting on information about the effectiveness of an organization’s chosen improvement program. | Improvement Program Assessment | IPA |
Kaizen | A Japanese word often thought of as “continuous improvement”. A deeper looks reveals how kai means “to take apart” and zen means “to make good”. | What is Kaizen? | |
Kaizen Blitz | Kaizen is a Japanese word and can be thought of as continuous improvement. Blitz is a German word for lightning fast. Thus, Kaizen Blitz is lightning fast continuous improvement. It is often a team event focused on improving one activity or step in a value stream. | What is Lean? | |
Key Performance Indicator | A performance measurement or metric that is thought to be a critical measure of success for an enterprise. Key Performance Indicators can be qualitative or quantitative in nature, and ideally, a leading indicator of progress. They can be dangerous when they drive individuals make the numbers look good regardless of the consequences. | Performance Indicator | KPI |
Lean | The systematic elimination of waste. Lean is far and away the number 1 organization improvement program in the world today. | What is Lean? |
Term | Definition | Link | Acronym |
---|---|---|---|
Lean and Green | The systematic elimination of unsustainable practices. This version of Lean adds environmental waste to the 7 classic types of waste which need to be eliminated. | What is Lean? | |
Lean Charlatan | Someone who may, or may not, have used Lean tools for chaotic cost cutting. They hold themselves out as experts at Lean when they have little to no knowledge about the principles, concepts, and techniques used for crafting a sustainable organization. | Lean Charlatan | |
Lean Six Sigma | A term with no clear meaning in the world of organizational improvement. It’s meant to sound like a hybrid program using Lean and Six Sigma. Most often, it is 95% Six Sigma with 5% Lean thrown in for good measure. Recent indications point to a race to the bottom where people do their own thing and call it Lean Six Sigma. They cut corners on the DMAIC steps from Six Sigma and don’t work the cultural transformation aspect from Lean. | What is Lean Six Sigma? | LSS |
Lean Transformation | Leveraging Lean principles, concepts, and techniques to craft a sustainable organization. | What is Lean? | |
Low Hanging Fruit | The obvious or easy things which can be done quickly and demonstrate success. Most improvement programs, such as lean or six sigma, will get off to a fast start by going after the low hanging fruit. | The Dangers of Low Hanging Fruit |
Term | Definition | Link | Acronym |
---|---|---|---|
Minimum Viable Product | A version of a new product with just enough features to be usable by early customers who can then provide feedback for further development. A minimum viable product has just enough core features to effectively deploy the product, and no more. It is typically deployed to a subset of possible customers, such as early adopters who are thought to be more forgiving, more likely to give feedback, and able to grasp a product vision from an early prototype or marketing information. | Minimum Viable Product | MVP |
Mistake Proofing | The process of applying a particular set of techniques to prevent and/or detect errors as early in a process as possible. AKA Poka-Yoke | Mistake Proofing | |
Operational Excellence | An approach to business management that emphasizes continuous improvement across all aspects of the business and within all business processes by creating a culture where management and employees are invested in business outcomes and empowered to implement change. | Operational Excellence | OpEx |
Overall Equipment Effectiveness | A powerful performance measurement derived from three elements: availability, performance, and quality. Measuring Overall Equipment Effectiveness is a best practice and very common in organizations leveraging improvement programs such as Six Sigma or Lean Transformation. | What is OEE? | OEE |
Plan, Do, Check, Act | A problem solving tool used for continious improvement which leverages the scientific method concepts of hypothesis, experiment, and evaluation. | What is PDCA? | PDCA |
Term | Definition | Link | Acronym |
---|---|---|---|
Poka-yoke | A Japanese term for “mistake proofing” which is a process of applying a particular set of techniques to prevent and/or detect errors as early in a process as possible. | Mistake Proofing | |
Project Champion | The person who owns the leadership role and delegates the project management role. A successful project champion brings organizational credibility, methodology knowledge, industry knowledge, and coaching skills. | Project Champion Guidelines | |
Quality Function Deployment | A structured approach and set of tools used to define customer requirements and convert them into detailed specifications and plans to produce the products and services which fulfill those requirements. | What is QFD? | QFD |
Return on Investment | A performance measure used to evaluate the efficiency or profitability of an investment. The benefit (or return) of an investment is divided by the cost of the investment and the result is expressed as a percentage. In project management, return on investment is used to quantify the financial benefits of the project vs. the cost and is often a key element in the approval to proceed. | Lean Project Scorecards | ROI |
Root Cause | The underlying fault or weakness in a process or system which triggers an undesired event or result. It is something you can change which will make an issue go away and not happen again. It must be something which is actionable. | Root Cause Analysis |
Term | Definition | Link | Acronym |
---|---|---|---|
Root Cause Analysis | Taking an issue, which needs to be addressed, and finding the root cause of the issue. The goal is to get to the source of the problem by focusing on the underlying causes of problems rather than simply treating the symptoms. | Root Cause Analysis | RCA |
Scrum | An agile team framework used to drive the completion of incremental work products in timeframes called sprints. It’s commonly used to develop software, but can be used for many other applications. | Scrum.org | |
Single Minute Exchange of Dies | A systematic approach to reduce changeover time, with the original focus on changing dies for stamping equipment. Today’s more inclusive terminology refers to this as changeover reduction. | What is Changeover Reduction? | SMED |
Six Sigma | A structured approach for improving the quality of products, services, and processes by reducing variation with a goal of reaching less than 3.4 defects per million opportunities to have a defect. | What is Six Sigma? | |
Standard Work | A purposeful articulation, of the current state of the work, with a focus on achieving an intended outcome, while providing a baseline for continuous improvement. | What is Standard Work? |
Term | Definition | Link | Acronym |
---|---|---|---|
Statistical Process Control | The application of statistical methods to monitor and control a process. Data is collected in the form of product or process measurements or readings from various machines or instrumentation. It is a scientific visual method to monitor, control, and improve the process by eliminating special cause variations. | Control Charts | SPC |
Supply Chain Management | The management of a network of interconnected organizations engaged in the provision of product and service packages required by the ultimate consumer. | What is Supply Chain Management? | SCM |
Sustainability | Meeting the needs of the present without compromising the future. | What is Lean? | |
The 5S System | A systematic approach to create and maintain workplace organization using the steps sort, stabilize, shine, standardize, and sustain (or some version of those words). Some advocates of Lean suggest this is a fast and easy thing you should do right away. Others will caution how the standardize and sustain steps are challenging and you should avoid starting a Lean program with a failure. | 5S Failure | 5S |
Total Productive Maintenance | A holistic approach to equipment maintenance that strives to achieve perfect production. The focus is on no breakdowns, no small stops, no slow running, no defects, and no accidents. It blurs the distinction between the roles of production and maintenance by placing a strong emphasis on empowering operators to help maintain their equipment. | Lean Thinking and Methods – TPM | TPM |
Term | Definition | Link | Acronym |
---|---|---|---|
Value Stream | All activities (value add, business value add, and non-value add) required to meet a customer or stakeholder request. | What is Value Stream Mapping? | |
Value Stream Map | A visual representation of activities and flows of information, materials, and services required to accomplish specific objectives. | What is Value Stream Mapping? | VSM |
Value Stream Mapping | A team based systematic approach to create value stream maps which identify waste in the current state or paint the vision of a future state with less waste. A current state and future state map are created, with the gaps between the two states becoming improvement projects. | What is Value Stream Mapping? | |
Voice of the Customer | A detailed set of customer wants and needs, organized into a hierarchical structure, and then prioritized in terms of relative importance and satisfaction with current alternatives. Voice of the Customer typically consists of both qualitative and quantitative research and is generally conducted at the start of any new product, process, or service design initiative. | Voice of the Customer | VOC |
Waste | An instance of using or expending something carelessly, extravagantly, or to no purpose. The 7 classic types of waste are Defects, Movement, Inventory, Poor Processing, Waiting, Over Production, and Motion. Two additional types of waste which are gaining acceptance are Underutilized Employee Capabilities and Environmental Waste. | What is Lean? |
Send us your favorite terms.
Get the Transformance Communiqué
“the newsletter for those crafting a sustainable organization”
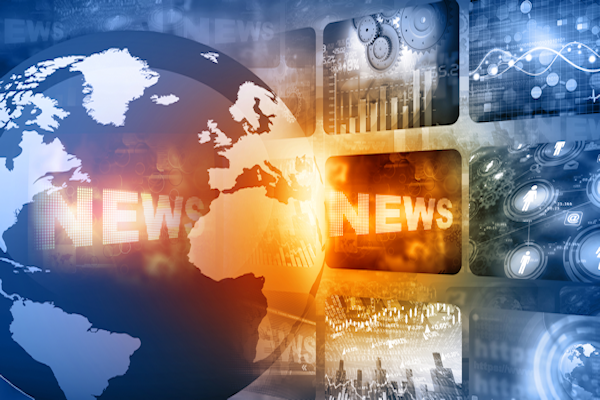
References
Unwinding Wordle: Accelerating Your Solve by Isaac Aronow.