By Mike Loughrin, CEO for Transformance Advisors
A Powerful Program
Six Sigma has earned a tremendous reputation as one of the leading organizational improvement programs. It has also remained a mystery to many.
A crisp definition is elusive and it seems you need to know the secret handshake in order to understand what people are talking about.
But, make no mistake, Six Sigma is a complete program with a powerful methodology. This methodology leverages strong statistical analysis and builds upon programs such as total quality management, statistical process control, and quality function deployment.
Emerging in the 1980s at Motorola, Six Sigma exploded in the 1990s with great success at General Electric, Allied Signal, and Honeywell. These early adopters become the legends of Six Sigma and saved billions of dollars in the process.
For this article, I’ll stick to standard Six Sigma. I won’t muddy the waters with Lean Six Sigma, Lean Sigma, Constraint Sigma, or some other derivative.
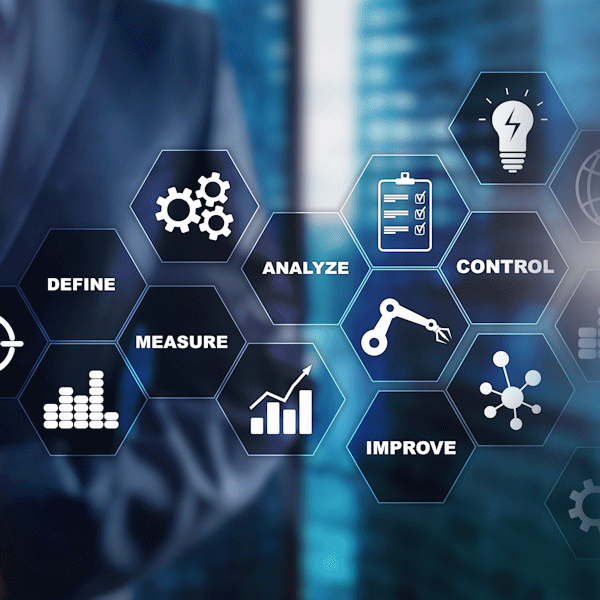
History Lesson
The beginnings of Six Sigma can be traced back to the early pioneers in the quality movement. These pioneers include the legendary names Shewhart, Deming, Juran, Ishikawa, Taguchi, and Crosby:
- Walter Shewhart developed statistical process control (SPC) and the plan, do, check, act (PDCA) process
- W Edwards Deming advanced a complete philosophy of quality management and the 14 points of quality
- Joseph M Juran evangelized the use of quality circles and was the first to apply the Pareto principle to quality
- Kaoru Ishikawa popularized the 7 basic tools of quality and developed the Cause and Effect Diagram – also called the Ishikawa Diagram
- Genichi Taguchi developed a methodology that emphasized “designing in quality” to reduce variation in manufacturing
- Philip B Crosby promoted the concept that “quality is free” and the need to establish a goal of “zero defects”
Early Champions
Trailblazers of the Six Sigma phenomena include names Smith, Harry, Bossidy, Galvin, Welch, and Walsh:
- Bill Smith is regarded as the “Father of Six Sigma” for developing a standard problem solving method that reduced defects at Motorola
- Michael Harry created a training curriculum at Motorola at the concept of Six Sigma roles defined as “belts” similar to the martial arts
- Larry Bossidy, as CEO for Allied Signal, brought rigor to the project selection process and defined a role for executives called “Champion”
- Bob Galvin led the way for executive engagement by launching the “Six Sigma Quality Program” at Motorola and establishing the goal tied to everyone’s performance assessment
- Jack Welch, as CEO for General Electric, promoted Six Sigma by creating training centers and helping deliver over $12 billion in savings – making Six Sigma world famous and the “rock star” of improvement programs
- Jodi Walsh energized process improvement for Lexmark International by creating an effective problem solving program with coaches, problem solvers, and engaged employee teams.
“Quality is not an act, it is a habit.”
– Aristotle
What Does Six Sigma Mean?
To understand Six Sigma, you need to start with the meaning of the words.
Six is easy. but more to come on that later.
Sigma is the 18th letter of the Greek alphabet and is used by statisticians to designate the term “standard deviation”.
Calculating the standard deviation is a way to identify the amount of variation in a product, service, or process.
For example, you could weigh 1,000 candy bars. The average weight could be 1 ounce, but most will be plus or minus some small amount. If there is a large amount of variation, the standard deviation will be high. Conversely, if everything is working well, there will be a small amount of variation and the standard deviation will be low.
Statisticians have figured out the math and I won’t go into the details here. What they have proven is that, for a normal distribution, the average plus or minus six standard deviations will be the actual measurement for 99.99966% of the total measurements.
The goal is to determine stakeholder expectations for quality and then implement processes which meet those expectations 99.99966% of the time.
That’s what we mean by Six Sigma levels of quality.
Caution: the math is more complex and beyond the goal of this article.
But, we do need to explore one more aspect wrapped around the math.
“Quality is the result of a carefully constructed cultural environment.”
– Philip Crosby
Defects Per Opportunity
We just mentioned the need to determine stakeholder expectations. The specific requirement is to understand how much variation is acceptable.
Going back to our candy bar, let’s say we collect feedback from consumers, retailers, cost accounting, and the Food and Drug Administration.
Synthesizing the feedback, we determine our candy bars need to be plus or minus 0.05 ounce, or can range from 0.95 to 1.05 ounce.
We have our quality measure and now need to establish processes which can deliver!
Wrong. You are not done!
In Six Sigma lingo, a defect is anything which annoys a customer and an opportunity is any chance to be annoying.
There are many other attributes, besides weight, which reflect an opportunity to annoy a stakeholder.
Think about price, delivery, availability, packaging, sustainable practices, and don’t forget about taste.
Of course, there can be thousands of opportunities for many products, services, and processes. Six Sigma uses tools such as “critical to quality” to narrow the focus to what needs to be included.
“Quality means doing it right when no one is looking.”
– Henry Ford
Bring Home The Math
Back to that 99.99966% we covered earlier.
If 99.99966% are good, then 0.00034% are bad – the defects.
0.00034% is the same as saying 3.4 per million.
Bringing home the math – the goal of Six Sigma is to reduce variation to the point where you have less than 3.4 defects per million opportunities to have a defect.
Knowing the prior sentence makes you more knowledgeable about Six Sigma than most of the people you will meet at any holiday party!
And knowing that sentence, means you know the first competitive advantage Six Sigma has over other improvement programs.
“Uncontrolled variation is the enemy of quality.”
– W Edwards Deming
Competitive Advantage 1 – An Achievable Goal
While the statistics can cause confusion, I suspect the ability to leverage hard data about a product, service, or process is how Six Sigma captured the support of executives at the early adopters.
The fanatics for other improvement programs tend to proclaim unattainable goals such as zero defects, zero inventory, 110% customer delight, organizational perfection, or galactic optimization.
These over-the-top pipe dreams have never been able to rally an organization or get serious support from executives with the power to fund an improvement program.
While seeking Six Sigma quality is an extremely challenging goal, the math makes it seem possible.
You can imagine an executive saying “I understand you want to achieve 3.4 defects per million opportunities. How do you plan to achieve it?”
Competitive Advantage 2 – Structured Methodology
Having an achievable mathematical goal is just one benefit of Six Sigma.
The second competitive advantage of the Six Sigma program is a structured methodology. It comes as a 5 step process:
- Define
- Measure
- Analyze
- Improve
- Control
The trailblazers of Six Sigma designed these steps to support any level of complexity. The brilliance is how you always follow the same 5 steps. You simply grab different tools from the Six Sigma toolbox.
A project with massive amounts of data will leverage strong statistical analysis. A project with less data may use tools as simple as a check sheet and a scatter diagram.
Learning about the tools and where to use them is why Six Sigma training courses are so extensive and intense. The challenge is figuring out who to train and what tools to train them on.
This training challenge brings us to our third and final competitive advantage of the Six Sigma program.
Competitive Advantage 3 – Six Sigma Belts
Known as “belts”, Six Sigma training programs are classified by the level of training and the roles people will perform on project teams. These belts and the level of training are:
- Yellow Belts receive about 4 to 8 hours of training; everyone in an organization should get this amount of training which is not much more than you are reading in this article.
- Green Belts receive about 6 to 10 days of training; heavy on the 5 step DMAIC methodology and the most common problem solving tools
- Black Belts receive about 15 to 20 days of training; all the Green Belt plus a much deeper dive into statistical analysis and project management skills
- Master Black Belts take an additional 10 days beyond Black Belt training; intense statistical tools and program leadership competencies
- Champions take about 2 days of training focused on applying Six Sigma to business processes and deploying projects across an organization
A caution: there is no official curriculum of training requirements for each belt – it’s buyer beware when searching for training.
In terms of project roles:
- Yellow Belts will serve as subject matter experts and assist in other project support roles
- Green Belts will manage projects, collect data, analyze data, design improvements, implement improved processes, and monitor new processes
- Black Belts will lead major projects, ensure rigorous data analysis, coach teams in designing robust solutions, guide implementation of improved process, and monitor new processes until they are ingrained
- Master Black Belts will provide expert advice on overall program management and train new Black Belts
- Champions will be the executive sponsors for projects ensuring the right projects are funded and solutions provide benefits to the organization
A caution: there is no official alignment of belts and project roles – each organization should design and staff projects to meet their needs. Common sense tells you not to staff a “Six Sigma” project with people who have zero training and are filled with fear when it comes to statistical analysis.
Summary
Six Sigma has become one of the best improvement programs of all time and can lay claim to three competitive advantages:
- A specific goal to reduce variation to the point where you have less than 3.4 defects per million opportunities to have a defect
- A structured 5 step methodology which can flex and use different problem solving tools to meet the challenges of projects with different levels of complexity
- A comprehensive approach to training and project team roles using classifications referred to as “belts”
One potential weakness of Six Sigma is the lack of a generally accepted definition. It’s ironic to see how much variation exists when you search for the definition of a program focused on reducing variation!
What is Six Sigma?
Just one more item to complete!
Let’s establish a crisp answer to that question – “What is Six Sigma?”:
Six Sigma is a structured methodology for improving the quality of products, services, and processes by reducing variation with a goal of reaching less than 3.4 defects per million opportunities to have a defect.
That feels like an accomplishment.
FAQs
How is Six Sigma different from Lean Six Sigma?
Research into Lean Six Sigma reveals it is much more about Six Sigma and tends to have very little about the rich features of a Lean Transformation. Lean Six Sigma adherents will often treat Lean as a collection of tools, you can sometime use when you work on a Six Sigma project.
Descriptions of Lean Six Sigma will often place a strong emphasis on using the Define, Measure, Analyze, Improve, and Control (DMAIC) methodology. This methodology is big for Six Sigma projects and not very common for Lean projects.
You can learn more at What is Lean Six Sigma?
Are there training programs for Six Sigma?
Yes, there are all sorts of training programs for Six Sigma. Our family of training and certification programs includes:
Certified Six Sigma Yellow Belt is the introductory certification and is designed for everyone in any organization using the Six Sigma improvement methodology.
Certified Six Sigma Green Belt is for those who will manage projects, collect data, analyze data, design and implement improvements, and promote continuous improvement.
Certified Six Sigma Black Belt is for those who will lead major projects, ensure rigorous data analysis, coach teams in designing robust solutions, guide implementation of improvements, and monitor new processes until they are ingrained.
You can learn more at Six Sigma Belts.
We tried and failed with a Six Sigma program. Should we try again?
The answer is yes, only if you are willing to conduct a lessons learned appraisal and then set yourself up for success by establishing an effective organization improvement program. Don’t waste everyone’s time with some program of the month.
Your improvement program should have a goal where everyone is empowered to participate in improvement projects, problem solving efforts, and continuous improvement activities.
You should also evaluate the possibility that a Lean Transformation program could be a better approach for your organization.
We encourage you to learn about and take an Improvement Program Assessment.
We have hired multiple people with Six Sigma experience and they all have a different philosophy and approach. How can this be?
The good news is how Six Sigma is the #2 improvement program in the world. The bad news is how there are different flavors of Six Sigma all over the world.
If you have hired a number of people with Six Sigma on their resume, then chances are you have introduced variation, and possibly some chaos, into your organization. Some places think Six Sigma is just about product quality and you only work on quality issues. Other places use Six Sigma just for solving problems. The worst organizations will use the Six Sigma tools for chaotic cost cutting.
The newer challenge comes from those who think their Lean Six Sigma training makes them experts at both methodologies. These people are often thin on both Lean and Six Sigma knowledge.
Regardless of their background with Six Sigma, you need to ensure all new hires are educated on your organizational improvement program. You should even look at sending the new hires through the same training courses you use for those without any experience with Six Sigma.
I’m wondering if Lean Transformation is a better approach for my organization. What should I do?
First give yourself a pat on the back for realizing you have options.
Then, read What is Lean?
Then, read about our Lean Transformation Program.
Your next step is to contact us. We can help you assess your opportunities and craft a roadmap to success.
Mike Loughrin is the CEO and Founder of Transformance Advisors. He also teaches for Louisiana State University Shreveport and is on the board of directors for the Association for Supply Chain Management Northern Colorado.
Mike brings exceptional experience in industry, consulting services, and education. He has directed several Lean Transformation programs and has helped organizations such as Levi Strauss, Warner Bros., Cabela’s, Constellation Brands, Lexmark, and Sweetheart Cup.
Keeping a commitment to a balanced life, Mike loves downhill skiing, bicycle rides, and hiking in the mountains. See one of his trails of the month at: Little Switzerland.
What is Lean?
Six Sigma Belts
What is Lean Six Sigma?
Six Sigma Project Scorecards
What is Lean Transformation?
Subscribe to our newsletter
References
Six Sigma Belts, Executives, and Champions by ASQ
Six Sigma: Methodology and Belt Rankings by Adam Hayes
Organizational Improvement Acronyms by Transformance Advisors
Organizational Improvement Definitions by Transformance Advisors