By Mike Loughrin, CEO for Transformance Advisors
Make No Mistake
Don’t let anyone steer you wrong. Lean is “the #1 improvement program in the world”.
The only real competition for popularity comes from inaction or weak attempts which rely upon naive trial and error.
In terms of comprehensive programs, the runner up methodology is Six Sigma. It is a great program, but far less popular.
Let’s look closer at how Lean is working, for all types of organizations, in terms of:
- Foundation
- Focus
- Tools
- Vision
- Applicability
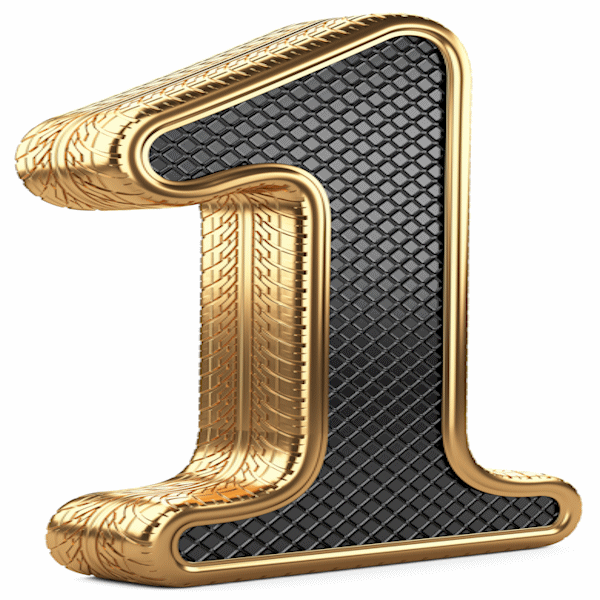
Lean is the clear leader as: “the #1 improvement program in the world”.
1. Foundation = Definition and Principles
Define Lean
Lean can be defined as “the systematic elimination of waste”.
The first key word is systematic – we are not interested in a chaotic scramble.
The second key word is waste – we are not going for a cost cutting frenzy.
It takes a systematic approach to find and eliminate the root causes, which create the waste, found in all organizations.
Any fool can cut costs (and revenue) to zero.
Lean is far more effective than chaotic cost cutting efforts.
Lean is: “the systematic elimination of waste”.
Lean Principles
There are 5 principles of Lean. These 5 principles were first articulated in the bestselling book “Lean Thinking” by James P. Womack and Daniel T. Jones. The 5 principles are:
- Specify Value
- Identify Value Streams
- Create Flow
- Leverage Pull
- Seek Perfection
A principle is a fundamental truth. If you are serious about Lean, then you should be leveraging these principles. If you are not serious, then ignore these principles at your own peril.
One caution is to understand how these fundamental truths are guiding principles while you work to eliminate waste. Unlike many other methodologies, Lean principles are not a sequence of steps, or milestones, you need to accomplish. You can specify value and identify values streams at the same time. You can create flow and leverage pull at the same time.
A fundamental truth is simply something you must do.
The foundation of Lean is: “the systematic elimination of waste by practicing the 5 principles of Lean”.
2. Focus = Value vs. Waste
Types of Value
Lean views all activities in terms of the type of value they create.
There are 3 types of value:
- Value Add: Activities which are necessary for meeting customer requirements
- Business Value Add: Activities which are necessary for meeting other stakeholder requirements
- Non-value Add: Activities which are not valued by any stakeholder
While it sounds simple, value can be challenging. One customer will value one thing and another will value something else.
Beyond customers, contemporary Lean enthusiasts understand how many other stakeholders value what their organization does. It would be foolish to ignore owners, employees, investors, your local community, and many other stakeholders.
“An economist is someone who knows the price of everything and the value of nothing.”
– misquote of Oscar Wilde
Types of Waste
Lean is focused on eliminating all types of waste.
The 7 classic types of waste are:
- Defects
- Movement
- Inventory
- Poor Processing
- Waiting
- Over Production
- Motion
As Lean evolves, two other types of waste are gaining acceptance:
- Underutilized Employee Capabilities
- Environmental Waste
Waste can be defined as “an instance of using or expending something carelessly, extravagantly, or to no purpose”. For Lean enthusiasts, waste is found in those non-value add activities.
Waste is: “an instance of using or expending something carelessly, extravagantly, or to no purpose”.
3. Tools
There are a large number of tools which are used to systematically eliminate the types of waste.
Some of the commonly used tools include:
- Value Stream Mapping
- A3 Problem Solving
- Changeover Reduction
- The 5S System
- Standard Work
- Visual Controls
- Mistake Proofing
Many of these tools will be used by employees working in teams during Kaizen Blitz events.
Kaizen is Japanese and can be thought of as continuous improvement. Blitz is German for lightning fast. Kaizen Blitz is lightning fast continuous improvement.
“If all you have is a hammer, then every problem looks like a nail.”
– attributed to Mark Twain (based upon no evidence whatsoever)
4. Vision = Lean Transformation
Everyone is Empowered
A key aspect of the Lean vision is to make a transformation where everyone is empowered to participate in waste elimination projects, problem solving efforts, and continuous improvement activities. In other words, employees “make independent decisions and take action as they see fit”.
Beyond empowerment, a growing number of leaders see the opportunity to create a better quality of work life for their organizations.
Processes filled with waste do not provide the value sought by customers and other stakeholders. The “work” for people trapped in broken processes is frustrating, exhausting, and unrewarding.
These broken processes are often found at smaller organizations which have grown to the point where tribal knowledge no longer works. You can also find broken processes at larger organizations which have downsized the number of employees, but not the amount of work.
A Lean assessment is an ideal technique for organizations to track their progress with a transformation. It quantifies how the culture is changing as an organization journeys through a transformation. You should measure progress in terms of leadership, knowledge, teamwork, alignment, and results.
Empowered employees: “make independent decisions and take action as they see fit”.
Sustainable Organizations
Crafting a sustainable organization is the ultimate objective of a Lean Transformation program. A sustainable organization “achieves its mission while meeting the needs of the present without compromising the future”.
This requires creating:
- A culture where all functional areas are completely committed
- Alignment from suppliers to customers using proven best practices and emerging trends in relationship management
- Rock solid support for all value streams in terms of leadership, knowledge, and teamwork
- Performance and results which meet customer and other stakeholder value agreements
Two key responsibilities for a leadership team are to:
- Create the vision of a sustainable organization
- Define a Lean Transformation program as a strategic initiative
A sustainable organization: “achieves its mission while meeting the needs of the present without compromising the future”.
5. Applicability = Everyone and our Planet
Lean Transformation for Everyone
Lean is an all inclusive improvement methodology and is growing rapidly in all types of organizations. No one is being left behind.
You can find success stories in terms of:
- Healthcare Services
- Product Development
- Maintenance
- Human Resources
- Manufacturing
- Customer Service
- Supply Chain
- Sales
- Food Service
- Engineering
- Logistics
- Retail
- Information Technology
- Financial Services
- Field Service
- Marketing
- Hospitality Services
- Sourcing
- You
Leaving No One Behind: “Lean is an all inclusive improvement methodology which works for any organization.”
Lean and Green
The tools for Lean and the tools for Green are being blended to provide a powerful toolkit for Lean and Green.
We define Lean and Green as “the systematic elimination of unsustainable practices”.
Adding environmental waste to the 7 classic types of waste is a powerful enhancement to the goal of saving our planet. The Environmental Protection Agency defines environmental waste as “an unnecessary or excessive use of resources or a substance released to the air, water, or land which could harm human health or the environment”.
The most exciting aspect of merging Lean and Green is how organizations are creating a competitive advantage, while at the same time, having a positive impact on our environment.
“Anything else you’re interested in, is not going to happen, if you can’t breathe the air and drink the water.
Don’t sit this one out. Do something.”
– Carl Sagan
Summary for “What is Lean?”
Lean has earned the crown as the #1 improvement methodology.
Don’t be fooled by charlatans, who have simply been chaotic cost cutters. These clowns do not understand the principles, or fundamental truths, and the other aspects which make Lean so powerful. Success comes to those who take a systematic approach to the elimination of waste.
Look for key components:
- Principles of Lean are fundamental truths
- Focus on value and waste
- Using tools to eliminate waste
- Empowerment seeking to craft a sustainable organization
- Leaving no one behind including our planet
FAQs
How is Lean different from Lean Six Sigma?
Research into Lean Six Sigma reveals it is much more about Six Sigma and tends to have very little about the rich features of a Lean Transformation. Lean Six Sigma adherents will often treat Lean as a collection of tools, you can sometime use when you work on a Six Sigma project.
Descriptions of Lean Six Sigma will often place a strong emphasis on using the Define, Measure, Analyze, Improve, and Control (DMAIC) methodology. This methodology is big for Six Sigma projects and not very common for Lean projects.
You can learn more at What is Lean Six Sigma?
Are there training programs for Lean?
Yes, there are all sorts of training programs for Lean. Our family of training and certification programs includes:
Lean Apprentice is the introductory certification and is designed for everyone at an organization which is pursuing a Lean Transformation.
Lean Practitioner provides hands-on experience leading a value stream mapping project.
Lean Expert provides hands-on experience leading a problem solving project.
Lean Master walks through an assessment of your organization’s Lean Transformation program and helps you build an improvement roadmap.
You can learn more at Lean Education Standards.
We tried and failed with a Lean program. Should we try again?
The answer is yes, only if you are willing to conduct a lessons learned appraisal and then set yourself up for success by establishing a Lean Transformation program. Don’t waste everyone’s time with some program of the month.
Your Lean Transformation program should have goal where everyone is empowered to participate in waste elimination projects, problem solving efforts, and continuous improvement activities. Lean is not just continuous improvement. Lean is not just problem solving. Lean is not just waste elimination projects.
We encourage you to learn about and take an Improvement Program Assessment.
We have trained employees on some Lean tools and have seen minor success in cutting costs. What should we do different?
We define Lean as “the systematic elimination of waste”. Unfortunately, Lean tools are often used for chaotic cost cutting and the results are always less than what can be achieved by focusing on waste.
For example, you can focus on the cost of energy and work your heart out seeking to cut the cost of energy. Alternatively, you can focus on the energy you are wasting through poor processes and reckless activities. A change in your mindset means you switch from chasing pennies by cutting costs to scooping up dollars by eliminating waste.
If you have been focused on cutting costs, then your best approach is to educate your team on the benefits of a Lean Transformation. You need a program with a better focus on principles, types of value, types of waste, empowerment, and the goal on creating a sustainable organization.
We have hired multiple people with Lean experience and they all have a different philosophy and approach. How can this be?
The good news is how Lean is the #1 improvement program in the world. The bad news is how there are different flavors of Lean all over the world.
If you have hired a number of people with Lean on their resume, then chances are you have introduced variation, and possibly some chaos, into your organization. Some places think Lean is just about continuous improvement and you do simple things for 2 minutes every day. Other places use Lean just for solving problems or for value stream mapping projects. The worst organizations will use the Lean tools for chaotic cost cutting.
Regardless of their background with Lean, you need to ensure all new hires are educated on your Lean Transformation program. You should even look at sending the new hires through the same Lean training courses you use for those without any experience with Lean.
You can learn more at Lean Transformation Program and Lean Education Standards.
Lean looks like the solution we have been searching for. What should I do first?
First give yourself a pat on the back for realizing Lean can be transformative for your organization.
Then, read about our Lean Transformation Program.
Your next step is to contact us. We can help you assess your opportunities and craft a roadmap to success.
Mike Loughrin is the CEO and Founder of Transformance Advisors. He also teaches for Louisiana State University Shreveport and is on the board of directors for the Association for Supply Chain Management Northern Colorado.
Mike brings exceptional experience in industry, consulting services, and education. He has directed several Lean Transformation programs and has helped organizations such as Levi Strauss, Warner Bros., Cabela’s, Constellation Brands, Lexmark, and Sweetheart Cup.
Keeping a commitment to a balanced life, Mike loves downhill skiing, bicycle rides, and hiking in the mountains. See one of his trails of the month at: Little Switzerland.
Lean Education Standards
What is Plan Do Check Act?
What is Lean Transformation?
Recognizing the Need for Lean
What is Continuous Improvement?
Subscribe to our newsletter
References
Sustainability by Inchainge
Three Types of Value by Tom Cassidy
What is Lean? by Lean Enterprise Institute
Lean Thinking by James P. Womack and Daniel T. Jones
Lean Transformation by Bruce A. Henderson and Jorge L. Larco