By Mara Irons, Director of Marketing for Transformance Advisors
Is It Time?
In today’s fast-paced world, it’s vital to stay efficient and effective. However, many organizations encounter a variety of obstacles which might indicate it’s time for a Lean Transformation. Here’s how to identify if your organization needs a Lean Transformation.
Leadership should be attentive to specific buzzwords and phrases which often indicate deeper issues. If you regularly hear words like firefighting, frustration, challenges, confusion, and micromagement, it can be a signal that there are underlying inefficiencies a Lean Transformation can address.
The issues holding organizations back can be grouped into three categories:
- Quality of Life
- Scalability
- Sustainability
Let’s look closer at each one.
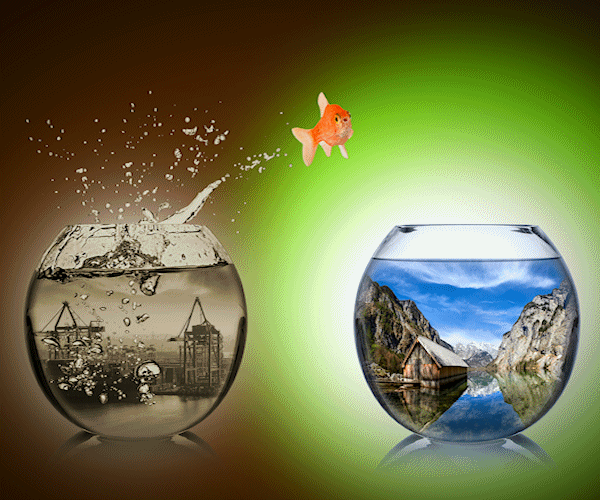
1. Quality of Life
A low quality of life at work is easy to spot and feel. You’ll notice it when:
- Firefighting is a normal daily routine
- The same problems come up over and over
- Turnover is high and good people are leaving
- Frustration runs high and hope runs low
Firefighting is a red flag. When teams spend their days reacting to urgent issues, it means underlying processes aren’t stable or reliable. This constant scramble pulls focus away from long-term goals and keeps everyone stuck in survival mode.
Recurring problems are another sign that something deeper isn’t being addressed. If the same issues keep popping up, it usually means temporary fixes are being applied instead of lasting solutions. Without root cause problem-solving, progress is impossible.
High turnover is a painful indicator that people are burned out or disillusioned. Your best employees, the ones eager to improve and make a difference, are often the first to leave when it becomes clear that their efforts aren’t making an impact.
Frustration builds quickly in an environment filled with chaos and repeat problems. Over time, it chips away at morale, and teams lose hope that things will ever improve. No one signs up for a job expecting daily stress and little progress.
Noticing these signs is the first step toward improvement. A Lean Transformation helps eliminate the root causes of burnout and frustration, freeing your team to focus on meaningful, mission-driven work.
2. Scalability
Scaling your organization to meet bold goals takes more than ambition. It takes systems that support growth. You might have a scalability problem if:
- Micromanagement seems to be the only way to get things done
- There are too many meetings which chew up valuable time
- Only 1 or 2 people know how to do certain things
- People have to wait around for someone to OK the next move
Micromanaging doesn’t just frustrate employees, it also wastes managers’ time. Giving people clear responsibilities and the freedom to act builds trust and frees up time to focus on growth.
Meetings should be productive, not just frequent. A simple agenda keeps everyone focused, prepared, and on track. Without one, meetings often become just another time sink.
When knowledge lives within only a few people, it’s nearly impossible to scale. Documenting processes, like how to fix a machine or onboard a new client, makes knowledge available to everyone and reduces bottlenecks.
While some approvals are necessary, waiting shouldn’t bring everything to a halt. Look for what can move forward in the meantime. Even a Gemba walk can uncover opportunities to improve while you wait.
If you don’t have time to work on scaling, that’s a signal in itself. Lean gives you that time back by removing waste and making space for what’s important.
3. Sustainability
Most organizations seek to be sustainable and are not seeking to go out of existence. You can’t “achieve your mission while meeting the needs of the present without compromising the future” when:
- Processes are not up to the challenges of meeting stakeholder requirements
- Measurements drive the wrong behavior and set you back when people do what is rewarded
- There is no time to work on the strategy, if there even is a strategy
- People are unsure about the real needs of external or internal customers
When processes fall short of stakeholder expectations, trust erodes. Mistakes, delays, and missed targets add up quickly. A sustainable organization builds processes that are reliable, repeatable, and capable of meeting requirements consistently.
Metrics matter, but only if they encourage the right behaviors. When people are rewarded for hitting the wrong targets, they’ll do what’s measured, not what’s meaningful. Misaligned metrics can push teams to cut corners or focus on short-term wins at the expense of long-term success.
Strategy often gets sidelined in the rush to meet daily demands. But without time carved out for strategic thinking, organizations drift. A sustainable organization prioritizes both today’s work and tomorrow’s direction, because reacting all the time won’t lead to lasting progress.
If people don’t understand what their customers, internal or external, actually need, their work will miss the mark. Sustainability requires clarity. Knowing what matters most to those you serve allows teams to focus on delivering real value, not just staying busy.
If sustainability feels out of reach, it may be time to step back and rethink how work gets done. Lean provides the tools to align daily actions with long-term goals.
Implementing Lean Transformation
A successful Lean Transformation requires commitment from all levels of the organization, especially leadership. Transformance Advisors offers a comprehensive Lean Transformation program that equips your team with the tools and knowledge needed to craft a sustainable organization. The key components of the program are:
- Lean Projects
- Continuous Improvement
- Program Management
Let’s look closer at each one.
- Lean Projects: Our research and experience has revealed the key to success is executing well-defined Lean projects. These projects must engage employees to eliminate waste and deliver significant improvements.
- Continuous Improvement: Lean projects will provide you better and stable processes. This is when you are ready to leverage continuous improvement to keep getting better and respond to the constant change swirling around you.
- Program Management: Maintaining a portfolio of improvement projects, communicating the exciting accomplishments, dealing with change management, and providing educational events for everyone are just some of the requirements for a successful Lean Transformation. You need a champion focused on your Lean Transformation program.
Visit Transformance Advisors Lean Transformation Program for more information.
A Lean Transformation is “the systematic elimination of waste with the goal of crafting a sustainable organization.”
Top 5 Benefits of a Lean Transformation Program
Return on Investment (ROI)
The investment in a Lean Transformation program is relatively modest. It takes time and money for Lean projects, continuous improvement, and program management. The results, or return, can be astonishing.
Thus, astonishing return divided by modest investment = outstanding ROI.
A few of your results could be:
- Reduce the cycle time for new product development creating faster time to market and increased revenue.
- Reduce defects and wasted effort creating more efficient processes with reduced cost.
- Improve service and quality leading to impressed customers and increased revenue.
- Cut down on mistakes and miscommunication creating a better quality of life with fewer hassles and firefighting.
- Create stable processes which don’t rely on tribal knowledge and can scale up for growing revenue.
- Develop empowered employees with a common language able to drive continuous improvement.
- Reduce the waste of energy and materials lowering your carbon footprint and delivering on your sustainability goals.
A Lean Transformation program delivers results. There is a reason Lean is the #1 improvement program in the world.
Quality of Life
Low morale, low productivity, and high turnover plague many organizations. Processes rely on tribal knowledge and firefighting. Processes breakdown when there is the smallest disruption. There are too many hassles, the ship is sinking, and quality of life is low.
It does not have to be that way. A Lean Transformation program will create processes which are stable, flexible, and able to meet stakeholder needs. Empowered employees will focus on data-driven decisions and leverage systematic methodologies which will mean problems get solved and don’t keep coming back. No more whack-a-mole.
Scalability
Processes which rely on tribal knowledge and firefighting will hold an organization back. Many find they cannot grow as everything seems to break at the slightest increase in customer demand.
It’s very common for an organization to grow to a point where the old processes no longer work and it’s time for a significant upgrade. This is the ideal time for a Lean Transformation. It’s time to understand what works and doesn’t work with the current state. The next step is to create a better future state which leverages best practices and is scalable.
Lean more about reaching the points where it’s time to upgrade your processes at: 7 Stages of Growth.
Sustainability
The goal of a Lean Transformation is to craft a sustainable organization which “achieves its mission while meeting the needs of the present without compromising the future”.
The greatest benefit from undertaking a Lean Transformation is fulfilling the mission of your organization in a manner which protects planet earth and all stakeholders.
Community
Lean is the #1 improvement program for a reason. As the most popular and best improvement program, there is a large community of organizations and individuals on the same journey as you. This brings a number on advantages:
- The tools exist and you don’t have to recreate the wheel or waste resources developing new methodologies or new classes
- You will develop a common language, built around the elimination of waste, creating empowered employees able to drive continuous improvement
- You will join those organizations who proudly claim they are members of the Lean community, creating a competitive advantage
- You will recruit better candidates with Lean experience and won’t be fooled by those who have only been chaotic cost cutters
Lean more at: What is Lean?
“Investing in a Lean Transformation will equip your teams to work together to implement sustainable processes.”
– Lale Lovell, PhD, Vice President, Transformance Advisors
Summary
If your business frequently encounters challenges, firefighting, problems, confusion, miscommunication, and growth-related issues, it’s time for a Lean Transformation. Embracing Lean principles can lead to significant improvements in efficiency, quality, employee satisfaction, and overall business performance. By recognizing these signs and taking proactive steps through a Lean Transformation, you can craft a sustainable organization that will thrive.
Complete An Assessment Now
FAQs on What’s Involved with a Lean Transformation?
How do I know if my organization needs a Lean Transformation?
One easy way to recognize the need for a Lean Transformation is to look at and listen to what’s happening everyday. Common buzzwords or phases you might notice are:
- Challenges are confronting everyone. You are on defense all the time.
- Firefighting is the routine. Your best people are firefighters.
- Problem-Solving is fine, except when you keep solving the same problems over and over again.
- Confusion is driving people crazy. What should we do? Who should do something?
- Miscommunication leads to errors. I thought someone else was taking care of that.
- Room for Growth means you are not growing. Tribal knowledge is not effective and processes are sluggish.
You can learn more at: Recognizing the Need for a Lean Transformation.
Isn’t Lean just about making small improvements every day?
Making small improvements every day is just one part of Lean. As one of the easier things to do, some people choose to focus on it and ignore the higher value parts of a Lean Transformation.
Value steam mapping, problem solving, changeover reduction, the 5S System, and other Lean tools deliver big benefits. These are not small efforts where you spend 2 minutes a day.
Lean is the #1 improvement program in the world. The wide variety of tools and common sense indicates there is more to it than just making small improvements every day.
Those who only work 2 minutes a day are picking up pennies and stepping over bushel baskets of dollars.
You can learn more at: What is Lean?
We trained employees on some Lean tools and saw minor success in cutting costs. What should we do different?
We define Lean as “the systematic elimination of waste”. Unfortunately, Lean tools are often used for chaotic cost cutting and the results are always less than what can be achieved by focusing on waste.
It takes a change in thinking to focus on waste. Do you try to cut the cost of gasoline or do you stop wasting time and gasoline by combining trips or car pooling?
It often takes more training on Lean thinking vs. overdoing the training on Lean tools. You want to use the tools to eliminate waste. Don’t use the tools for chaotic cost cutting.
Using the tools correctly will come when you have the three components of a Lean Transformation in place. You need Lean projects, continuous improvement, and program management.
We have hired multiple people with Lean experience and they all have a different philosophy and approach. How can this be?
The good news is how Lean is the #1 improvement program in the world. The bad news is how there are different flavors of Lean all over the world.
If you have hired a number of people with Lean on their resume, then chances are you have introduced variation, and possibly some chaos, into your organization. Some places think Lean is just about continuous improvement and you do simple things for 2 minutes every day. The worst organizations will use the Lean tools for chaotic cost cutting.
Regardless of their background with Lean, you need to ensure all new hires are educated on your Lean Transformation program. You should even look at sending the new hires through the same Lean training courses you use for those without any experience with Lean.
You can learn more at: What is Lean?
Should we do Lean Six Sigma instead?
Research into Lean Six Sigma reveals it is much more about Six Sigma and tends to have very little about the rich features of a Lean Transformation. Lean Six Sigma adherents will often treat Lean as a collection of tools, you can use when you work on a Six Sigma project.
Descriptions of Lean Six Sigma will often place a strong emphasis on using the Define, Measure, Analyze, Improve, and Control (DMAIC) methodology. This methodology is big for Six Sigma projects and not very common for Lean projects.
If you want to do Lean, the #1 improvement program in the world, then do Lean. Don’t do Lean Six Sigma.
You can learn more at: What is Lean Six Sigma?
Can I just buy a magic pill which will optimize everything with no effort from our leadership team?
No!
It’s going to take a commitment from your leadership team.
Lean looks like the solution we have been searching for. What should I do first?
First give yourself a pat on the back for realizing Lean can be transformative for your organization.
Your next step is to contact us. We will help you assess your opportunities and craft a roadmap to success.
Mara Irons
Mara Irons is the Marketing Manager at Transformance Advisors. She specializes in crafting compelling content and conducting research to ensure community relevance. With a background spanning education, transportation, digital marketing, health, and nonprofit sectors, Mara brings diverse expertise to her role.
Driven by a passion for assisting small businesses in the digital realm, Mara delivers innovative solutions and fosters meaningful connections.
Outside of work, she loves exploring the outdoors with her dog, Indi. However, if it’s cold or raining, you can find her on the couch watching true crime documentaries with a glass of wine.
To learn more about Mara, visit her LinkedIn profile.
What is Lean?
Lean Education Standards
What is Lean Transformation?
What is Continuous Improvement?
Improvement Program Assessment
Subscribe to our newsletter
References
Lean Transformation by Bruce A. Henderson and Jorge L. Larco
Organizational Improvement Acronyms by Transformance Advisors
Organizational Improvement Definitions by Transformance Advisors