By Mike Loughrin, CEO for Transformance Advisors
Confusion Reigns
Educational courses and certification programs for Lean are all over the place. There are no generally accepted Lean education standards.
It’s ironic how a program focused on reducing waste has evolved into such uncontrolled confusion:
- Why does everyone have to waste time seeking to determine which concepts and tools should be taught to employees?
- Why are these charlatans running around treating Lean education as just an immersion into speaking Japanese?
- Who are these crazy people claiming it’s easy to change your organization’s culture?
For this article, I’ll stick to a standard Lean Transformation program. I will focus on the needs of those seeking to make the cultural transformation – the difficult path to creating a sustainable organization.
I won’t muddy the waters with Lean Six Sigma, Lean Sigma, Toyota stuff, or some other derivative. In addition, I will not be supporting anyone seeking to cause chaos with some fast cost cutting shenanigans. I will not be giving away a short list of magic bullets or a long list of a million foreign words.
A Solid Framework
Given an immense body of knowledge, you cannot, and do not need to, provide complete educational coverage to every person helping with a Lean Transformation. But, you do need to provide education to everyone and segment which concepts, terms, and problem solving tools should be taught to people, based upon their role in your Lean Transformation.
There are no “official” levels of knowledge for people working on a Lean Transformation. However, there is a common sense approach used by many organizations.
This common sense approach defines standards for education and the roles people will perform on Lean projects and other events. This widely used approach segments Lean education standards and the corresponding roles into the following:
- Apprentice: provide subject matter expertise and support projects, kaizen blitz events, and continuous improvement activities
- Practitioner: manage projects, lead value stream mapping sessions, and facilitate kaizen blitz events
- Expert: lead major projects, address complex problems, and advise project teams
- Master: establish standards, provide expert advice on overall program management, and coach problem solvers
- Champion: sponsor projects, ensure resources, and communicate the progress toward creating a sustainable organization
Of course, there is room at the margins. An organization might ask more, or less, from any role. This would simply mean more, or less, education would be required for succeeding at the assignment.
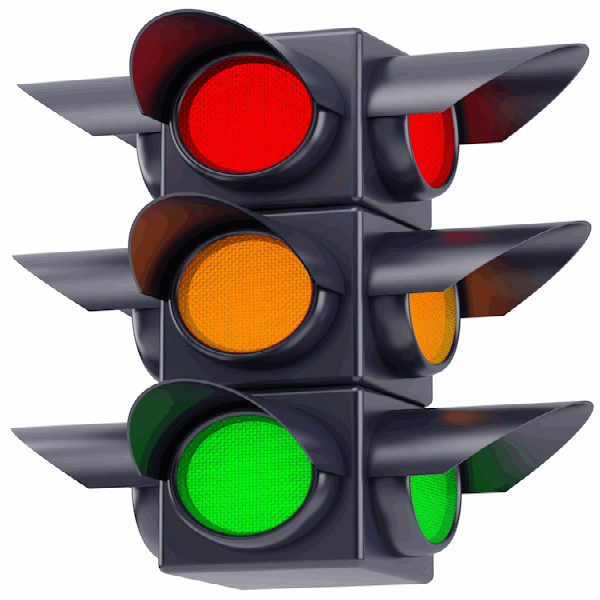
Knowledge Needs
Given the 5 Lean roles, let’s turn our attention to the education required for each role.
Warning: we are now at the point with very high risk of aggravating every Lean enthusiast who believes they have it figured out!
Those without a desire to learn – should stop reading now.
For those with the courage to continue, brace yourself and get ready to learn.
The balance of this article will explore the body of knowledge which, our research and experience demonstrate, should be included in the curriculum for each level.
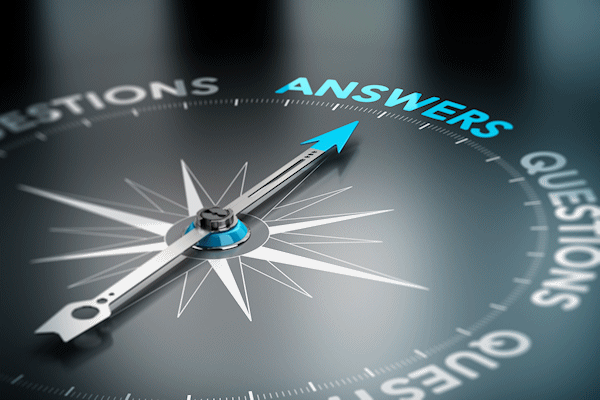
Apprentice
The curriculum for the Apprentice role should be a general introduction to key concepts and topics.
An organization specific class should include the case for change and explore successful Lean projects which have been completed.
Key concepts, terms, and tools for this role include:
- Principles of Lean
- Types of Value
- Types of Waste
- Continuous Improvement
- Standard Work
Practitioner
The curriculum for Practitioner education should include a deeper dive into everything covered for the Apprentice role. In addition, there should be a well-defined project which walks through the specific steps for one of the common systematic techniques such as value stream mapping, changeover reduction, or the 5S system. Value stream mapping is one of the best type of projects, for becoming a Lean practitioner, as this technique is associated with projects having a high probability of success.
Learning can be enhanced and accelerated when the project is a scripted example which includes data and information designed for learning the required concepts, terms, and tools. For example, an online simulation tool can provide quick access to a fictional organization with a current state full of waste. Students can apply what they learn to design a future state and see the impact of their decisions through simulation.
Key concepts, terms, and tools for this role include:
- Project Charters
- Mapping the Current State
- Assessing Opportunities
- Designing the Future State
- Implementation of Improvements
- Seeking Perfection
Expert
The curriculum for Expert education should include a Lean project which requires rigorous use of problem solving techniques. The project should tackle a complex problem where a solution has been elusive.
Learning should be supported through coaching from a qualified instructor. Successful problem solving leverages the two roles of problem solver and coach.
Key concepts, terms, and tools for this role include:
- Problem Statements
- Articulating the Current Situation
- Root Cause Analysis
- Developing Countermeasures
- Implementing Changes
- Creating Standardization
Master
Great news for those aspiring to the Master role. There are just a few additional requirements. However, these require skills such as leadership, coaching, and teaching.
The additional requirements include:
- Manage the Lean program for an organization, business unit, local site, or whatever
- Ensure Lean projects are selected, scoped, and executed appropriately
- Coach others through value stream mapping and problem solving projects
- Be the reservoir of knowledge for complex, but seldom used, problem solving tools
Key concepts, terms, and tools for this role include:
- Organizational Assessments
- Lean Program Management
- Lean Leadership
- Performance Management
- Engaging All Stakeholders
- Trends in Lean
Champion
A Lean Champion needs to provide sound advice on organizational needs and be skilled at developing others. The best leaders develop the next generation of leaders.
Requirements for this role include:
- Making, refining, and communicating the case for change and the transformation strategy
- Motivating and challenging people to improve themselves and the organization
- Understanding the strong ROI for the Lean Transformation and the even greater benefits from creating a great place to work
- Keeping the focus on changing the culture to create a sustainable organization
- Leading an annual effort to “step back to reflect” on progress and make course corrections
Summary – Lean Education Standards
I don’t expect to eliminate all of the confusion in the worldwide market for Lean education courses and certification exams. Most likely, I have made a number of experts turn red with anger. They are free to hold onto their own opinions.
My goal, for readers, is to provide a way to sort through the chaos and find a baseline for comparing Lean education courses and certification exams.
Credential Registry
We are members of the Credential Registry, an organization dedicated to providing up-to-date information about all credentials, a common description language to enable credential comparability, and a platform to search and retrieve information about credentials.
The best credentials are found at the Credential Registry.
Learn more at Credential Registry.
Mike Loughrin is the CEO and Founder of Transformance Advisors. He also teaches for Louisiana State University Shreveport and is on the board of directors for the Association for Supply Chain Management Northern Colorado.
Mike brings exceptional experience in industry, consulting services, and education. He has directed several Lean Transformation programs and has helped organizations such as Levi Strauss, Warner Bros., Cabela’s, Constellation Brands, Lexmark, and Sweetheart Cup.
Keeping a commitment to a balanced life, Mike loves downhill skiing, bicycle rides, and hiking in the mountains. See one of his trails of the month at: Little Switzerland.
Professional Certifications
Recognizing the Need for Lean
What is the Credential Registry?
Top Reasons to Earn a Certification
Lean and Six Sigma Talent Demand
Subscribe to our newsletter
References
Lean Thinking by James P. Womack, Daniel T. Jones
Organizational Improvement Acronyms by Transformance Advisors
Organizational Improvement Definitions by Transformance Advisors