By Jodi Walsh, Guest Contributor
Three Two One
It was March 10th, 2018. I looked like a serious professional hard at work on my computer. Surreptitiously, I had a little window, open on my desktop, keeping watch on a steaming behemoth ready to take flight. Every once in a while, a couple of “talking heads” would come onto the screen to amp up the audience concerning the spectacle at hand. I could hear colleagues down the hall doing the same thing.
The launch of the Falcon Heavy rocket from SpaceX.
Be still my heart.
And then, the glorious rocket rose majestically into the air. I thought about how anyone, for a cool $90M, could put 64 metric tons up there into the sky.
Commercial rocket launching was here.
It was spectacular. And then – the launch rockets returned to earth. Two of three landing to launch another day. Completely mind boggling, when you consider the sheer immensity of the engineering task. It seems miraculous they had a 66% success rate on those re-usable rockets. The experts had said it couldn’t be done.
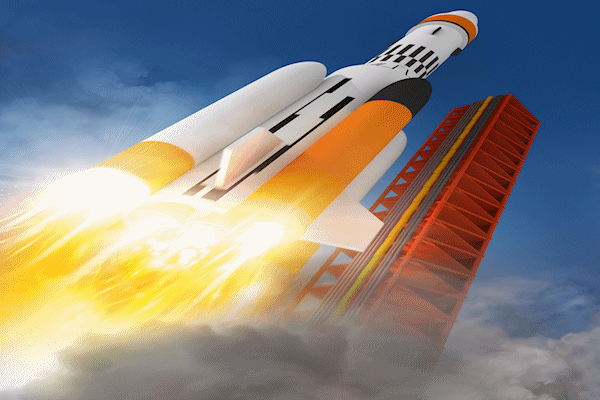
Rockets, Lean, and Six Sigma
I have a dear friend who worked for United Launch Alliance, the company that builds the Atlas engines which power the Falcon Heavy into the sky. I had the chance to visit that manufacturing floor several years ago. Since I am both a science geek, and an operations hound, I was completely fascinated by the dynamics of the work.
We spoke about many things, including Lean and Six Sigma.
It was a real education to learn how the rate of continuous improvement, which is sought by many Lean enthusiasts, is child’s play when compared to the advancements required for the achievement of commercial space endeavors.
It was equally amazing to discover how a Six Sigma error rate is considered a disaster for a rocket scientist. Nine sigma is the standard defined by the sign on the wall.
It is not that Lean and Six sigma disciplines are not valuable and necessary. It’s how the space industry has taken their own pursuit of continuous improvement and seeking perfection to a level which might have seemed delusional in the past.
The level of cumulative and sustained improvements which were necessary for the launch of the Falcon Heavy astound me.
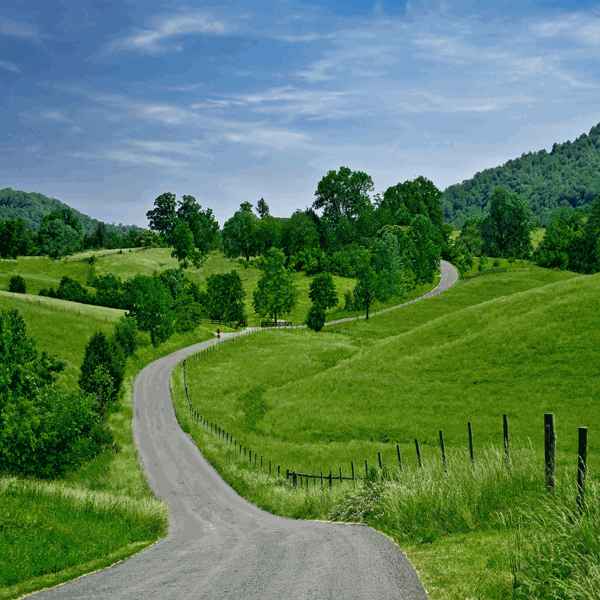
Not Just for Space
While the space industry has visible and disastrous consequences to a lack of perfection, it is not the only industry where defining standards and capturing successful changes is critical.
Every industry and every job task has an intended outcome. It is this intended outcome we all have in common. Beyond launching a rocket, other examples include heart surgery, automobiles, printed reports, happy hotel guests, a cup of coffee, or a cat rescued from a tree.
Everyone’s work effort has an intended outcome. The challenge becomes achieving this intended outcome every time. This is where the concept of standard work becomes a foundation for success, whether for rocket engines or a cup of java.
As we explore achieving the intended outcome, each and every time, let’s consider a definition of standard work.
“A purposeful articulation, of the current state of the work, with a focus on achieving an intended outcome, while providing a baseline for continuous improvement.”
– A Definition of Standard Work
Key Concepts
The three important concepts in the definition are:
- Purposeful Articulation
- Intended Outcome
- Baseline for Improvement
Let’s look closer at each one.
Purposeful Articulation
An individual worker needs to know how to perform their job in order to achieve the intended outcome.
By its very nature, the workplace is dynamic. Equipment ages, market expectations shift, product mix varies, worker skill sets evolve, regulations change, technology advances, and competitors innovate. You can probably keep this list going!
It can often be perceived that one standard approach is a laudable discipline. Compliance with a standard practice is seems like the best thing to do. But, the expectation for a single defined standard for any given work is too simplistic. For example, a tall person may be able to reach the can of beans on the top shelf. A shorter person may need to use a step ladder. Should we have standard work which requires everyone to use a step ladder?
Purposeful articulation seeks to produce stable outcomes rather than rigid processes. We want the can of beans retrieved safely from the top shelf. Standard work should not be confused with monolithic commonization.
Practically, the purposeful articulation of standard work includes three categories:
- Sequence
- Timing
- Work-in-process
Sequence
Most processes have a practical sequence of work, which is required to deliver the targeted results. Some work has an absolute sensitivity to the order of events – each step must be occur as specified. Other types allow for greater flexibility – the sequence is not important.
An effective definition must identify the optimal sequence of work, including the details of equipment, materials, information, and people.
Timing
Every process, whether informational, creative, managerial, or mechanical, has an appropriate time associated with it. Lean seeks to eliminate the time lost to waiting or other wastes, while Six Sigma will focus upon the variation in the time required for each step.
Awareness and specification of the time, each step takes, is important to a rigorous definition of standard work.
Work-in-process
Every process has an optimal amount of work-in-process. This work-in-process can be an easy and visible signal that a process is running effectively. Too much work-in-process hinders the cycle time. Too little can hamper the steady flow of output.
An awareness and definition of the optimal work-in-process is inherent to providing the purposeful articulation we seek.
Intended Outcome
While the details of any process are generally important to the outcome – it is uniformity in outcome which is the target, not necessarily uniformity in process.
The most important aspect of work is the result, for it is the outcome which is valuable to the customer.
What is our customer seeking when they purchase our service or product? What do they value?
This value can be stated to a very granular level. Consider just one activity on a value stream map. How does this activity produce value? What is it about this action which is necessary?
For lean, the principle of specify value applies to each customer. The intended outcome needs to match the value specified by the customer of the work.
For six sigma, the goal is to reduce the variation in our outcome and achieve less than 3.4 defects per million opportunities to have a defect.
Achievement and Improvement
A purposeful articulation of the work is insufficient. A definition of the intended outcome is also not enough.
Recall how standard work is a purposeful articulation of the current state of the work with a focus on achieving our intended outcome while providing a baseline for continuous improvement.
The effectiveness of standard work is measured by “achievement of the intended outcome” and “improvement of the current state.” Remember – compliance to the standard work is not the goal.
The goal of our work is value creation and the context of our effort is the pursuit of perfection. Thus, the current iteration of any standard work is the next to last draft. Each subsequent version should demonstrate both rigorous understanding of the current state and provide a platform from which changes can be made. Each version of the standard work is like a stair step. It should provide a firm foundation for the next step.
One can envision a purposeful process by which changes to standard work are implemented. It is called standard work process for changing standard work. Not only does this constant continuous improvement yield tremendous results, it ensures we get the intended outcome every time, even if the world changes.
Back To The Launch
Consider the launch of the Falcon Heavy again.
There are over 6,000 employees at Space X. If 25% of them make 1 change to their work which contributed to the successful launch, then 1,500 changes will impact the next launch. How important do you think it is to manage changes to standard work? Do you think it is important for everyone to have the same understanding of how to make a change?
Nine sigma quality at every step? Important hardly seems to be a big enough word! 1,500 changes to a nine sigma process could be challenging.
How about the processes your surgical team follows? Does it matter that a team makes 100 changes between the last successful surgery and your surgery?
How about a cup of coffee or a pint of beer you enjoyed on the last visit to your favorite watering hole? Does it matter if the changes they make between the last brew and the next brew preserve your experience? How important is a purposeful articulation of the current state of the work? Do you want a great drink and consistency of experience?
Summary
Every job task has an intended outcome which is critical to achieve. They are not all life and death or worth billions of dollars.
But, every organization is fighting to meet the needs of many stakeholders.
Standard work is a foundational discipline for achieving the intended outcome and meet those stakeholder needs.
Just ask the NASA engineers who said “booster reuse is impossible” and what they now think after the SpaceX team has landed one on a barge in the middle of the ocean. Repeatedly.
One disciplined step at a time. One standardized disciplined step at a time.
Jodi is an innovator, with a passion for simplification of the complex and creating sustainable systems.
Formally educated at Northwestern University as a PhD Chemist, Jodi is an accomplished manager and leader with key strengths in manufacturing, supply chain, process engineering, and applied research and development.
With 23 years of experience at Lexmark International, she is recognized as a “go-to” person who directs work teams that exceed expectations and pursue continuous improvement. Jodi has developed people, products, processes, and organizations.
But, don’t think Jodi is all work and no play. She is a singer, gardener, home cook, and poet. She has a deep conviction that balancing professional time and personal time are critical to the well-being of people, processes, and organizations. Learning, technical rigor, innovation, and respect for the dignity of individuals are some of her highest values.
What is OEE?
What is Lean Transformation?
What is Changeover Reduction?
What is Value Stream Mapping?
Policies, Procedures, and Instructions
Subscribe to our newsletter
References
What is Standard Work? by Dozuki
Organizational Improvement Acronyms by Transformance Advisors
Organizational Improvement Definitions by Transformance Advisors