By Mike Loughrin, CEO for Transformance Advisors
A Continuous Improvement Tool
A key part of Six Sigma and Lean Transformations is empowering people to identify problems and make continuous improvement to processes and procedures. One common problem solving tool leveraged by many organizations is called Plan, Do, Check, and Act or PDCA.
But tread with caution! PDCA has evolved through the years and some confusion has crept into the DNA.
Warning! Danger lies ahead for Six Sigma and Lean experts who have crafted some alternative version of PDCA. You may become uncomfortable with the balance of this article.
PDCA is said to have originated as the Shewart Cycle, named after the concept originator Walter Shewart. The Shewart Cycle contained Plan, Do, and See.
Edward W. Deming modified the cycle to be Plan, Do, Study, and Act.
Refinements in Japan and the return of these ideas to the United States produced an evolution into what we now call Plan, Do, Check, and Act.
The spirit of the tool is to leverage the scientific method concept of hypothesis, experiment, and evaluation. Hypothesis = Plan, Experiment = Do, and Evaluation = Check. Then, if all is well, you can Act.
Let’s take a closer look at each of the four steps.
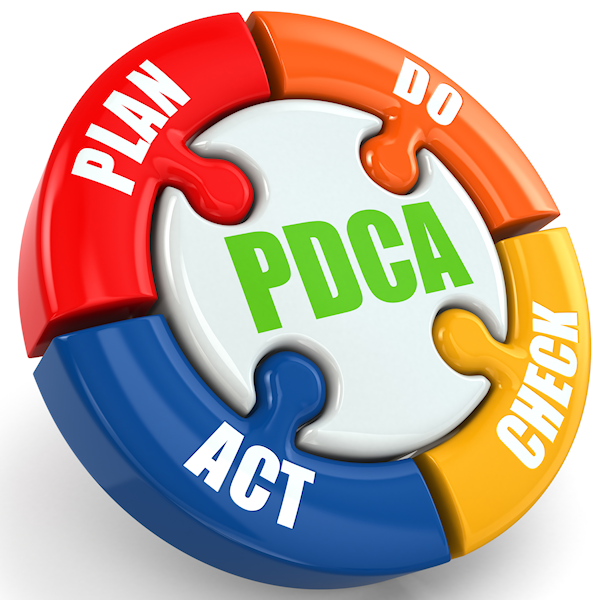
Plan
Identify the problem and develop a plan for improvement:
- Identify the problem
- Agree on the desired situation
- Determine the root cause(s)
- Select a potential solution
- Create implementation plan
There is a lot of work in the above activities. The Plan step can be 75% of the entire effort.
Some of the tools which can help during this step include:
- Brainstorming
- Cause and Effect Diagram
- 5 Why Questioning
- Run Chart
Do
Test your solution:
- Implement on a trial basis
- Take measurements
At this point, keep in mind that you are not “doing” a full implementation. You are only testing a possible solution.
This step can be confusing:
- One website claims Do is “about the implementation and realization of the planned improvements of the entire process”
- Going in the opposite direction, one over-priced workshop claims to teach you Do is “analyze the causes” and ignores any mention of running a trial to obtain measurements
Both of the above are classic examples where so-called experts are confusing the rest of us. The Do step is not about realization of improvements and it is not just about analyzing the causes.
If you stick with the evolution from the scientific method, then it’s clear Do is about Experiment. It’s not doing everything, in the scope of your Plan, nor is it just about analysis.
Check
Evaluate the results:
- Compare your measurements to expectations
- If problem persists, then return to the Plan step
- If success achieved, then proceed to the Act step
As we saw with Do, some charlatans sow confusion with everything they say. In one example, the know-it-all claims Check is about “improving the process” rather than analyzing the measurements from the Do step.
Staying with the scientific method, then it’s clear Check is about evaluation of the experiments regarding your hypothesis.
Act
Fully implement the solution:
- Update documentation on new standard work
- Train everyone in the new procedures
- Apply improvement to all areas
- Monitor performance
This step can also be confusing. Some call this Adjust. Others say this is React instead of Act. Someone even proclaimed the fourth step is Proact – whatever that means.
Hats off to those who have overcome the confusion and actually accomplish something!
One additional note is how many self-proclaimed gurus suggest you are never finished. They claim, that after you complete the Act step, you then return to the Plan step and begin again. At first glance, that sounds nice. But, it implies every PDCA you ever did is still active. Does this mean you could have hundreds, or thousands, of active PDCA teams working infinite loops?
Pros and Cons
PDCA is a problem solving tool many organizations use all the time. Others have struggled and not found value in the tool.
Let’s look at what some claim are the Pros and Cons:
Pros
- Tool is very easy
- Lots of people use it
- Only tool you need
- It works
Cons
- Steps are confusing
- Lacks sustainability
- Other tools are better
- It doesn’t work
I’m not a fan about most of the above Pros and Cons. The only one which resonates with me is “other tools are better”.
Summary
While Plan Do Check Act is often prescribed as a easy tool, reality is far different.
When and where to use PDCA is part of the issue:
- Some claim “PDCA is usually associated with sizable projects seeking breakthrough improvements”
- Others assert “PDCA should be used during kaizen blitz events seeking frequent small improvements”
- Still others announce “you should use PDCA everyday for every problem” – a violation of the common sense notion which tells us “if all you have is a hammer, then every problem looks like a nail”
Additional challenges include:
- The fine print for Plan suggests this first step is 75% of the total effort and is really multiple steps
- There is an assumption the Act step is not the end – the team is really, in an endless loop, repeating PDCA forever
- Historians warn us that, founded in 1884, the Painting and Decorating Contractors of America (PDCA) is a national trade association dedicated to the success of painting and decorating contractors through ethics, education, and excellence
What is Lean?
5 Horrors of Lean
What is Standard Work?
What is Lean Transformation?
What is Continuous Improvement?
Subscribe to our newsletter
References
Plan Do Check Act by MindTools
Organizational Improvement Acronyms by Transformance Advisors
Organizational Improvement Definitions by Transformance Advisors